Operational Excellence
The Appleton Greene Corporate Training Program (CTP) for Operational Excellence is provided by Mr. Muenzing Certified Learning Provider (CLP). Program Specifications: Monthly cost USD$2,500.00; Monthly Workshops 6 hours; Monthly Support 4 hours; Program Duration 36 months; Program orders subject to ongoing availability.
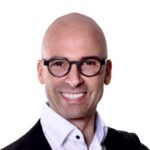
Personal Profile
Meet Mr. Muenzing: Visionary Leader in Lean Transformation and Turnaround Management
Mr. Muenzing is a distinguished authority in lean transformation and turnaround management, amassing three decades of executive and advisory roles in management consulting. As President of Leanmap, a specialized management consulting boutique, he empowers manufacturing, technology, and service enterprises to elevate performance and gain sustainable competitive advantages through world-class operations.
Driven by innovation and systems thinking, he earned a Bachelor’s in Electrical Engineering (BSEE) from FHD in Germany. He swiftly excelled in the Telecom industry, pioneering three groundbreaking innovations for base stations that showcased his visionary mindset and exceptional problem-solving skills. Recognizing the need for business acumen, he pursued a Master’s in Business Administration (MBA) from NSU in the USA, laying the foundation for his transformative leadership.
Throughout his illustrious career, he revitalized struggling companies and enhanced successful ones to reach world-class status. With extensive expertise in operations, product development, and business consulting, he offers diverse insights to clients. An accomplished author, he penned “The 20 Keys to World-Class Operations” and “From Chaos to Control.” He also shares his knowledge through speaking engagements on innovation, lean transformation, cost reduction, and quality excellence.
Mr. Muenzing’s expertise has been sought by over 150 client-organizations across 40 countries, driving operations toward world-class benchmarks. These transformations yielded financial benefits surpassing $500 million from top-10 programs, with an average return on investment (ROI) of 12x across all initiatives. With a remarkable 96% repeat clientele rate, his enduring impact is evident, leaving a lasting impression on clients. Key engagements include:
1. Leading Automotive Supplier (Sweden):
As an Industrialization Expert, led the Engineering team to enhance time-to-market (TTM), quality and delivery performance to major automotive customers. His systematic improvements in technology readiness and process capability led to a doubling of launch successes at the start of production (SOP) and an astounding 8x reduction in defects per unit (DPU) in just six months.
2. Major Semiconductor Fab (USA):
In the role of Operations Expert, spearheaded a transformation initiative to optimize cost-per-move (CPM) through adaptive maintenance, systematic problem analysis, and disciplined root-cause elimination. Coached 10 Advanced Module Engineering (AME) teams during the transition phase, realizing 326 projects that delivered $118 million cost savings (run rate) in the first year.
3. Pharmaceutical Operation (France):
As Operations Expert, led the factory turnaround with focus on operational efficiency (OEE) to ensure stable patient supply. As a result, doubled efficiency within 12 months, increased throughput 32% without spending capital, cleared backlog, reduced deviations by 25%, and shortened lead time by nearly 50%, while maturating the site towards Operational Excellence.
4. Largest Marine Electronics Company (Mexico):
As the Interim Operations Executive, he orchestrated a Manufacturing Turnaround that doubled throughput to meet customer demand. Through systematic defect reduction, design for manufacturability (DFM), and strict flow management, he achieved a 44% reduction in labor hours, 53% reduction in footprint, 94% reduction in inventory, and 66% reduction in rework in just one year.
5. Leading Flavor and Fragrance Company (Switzerland):
In the capacity of Global Leader for Lean and Operational Excellence, he spearheaded a Lean Transformation Initiative across 20 global flavor-production facilities. His efforts yielded over 400 improvement ventures, adding CHF 36 million to the company’s profits in just 3 years, while attaining a competitive edge by elevating both quality and delivery standards..
6. Largest Appliance Factory (China):
As the Integration Manager, he successfully merged two large assembly plants in Guangdong into one. Through streamlining material flow, balancing workload, and right-sizing manning, he reduced shortages and late deliveries by 50%, lowered on-hand inventories from 46 to 18 days, and added $20 million annual manufacturing capacity to meet forecasted demand.
Mr. Muenzing exemplifies impactful leadership through visionary expertise, driving lasting transformations by fostering world-class quality, speed, and efficiency. His consistent record of sustainable bottom-line growth and unwavering commitment to continuous improvement mark him as a global driving force behind corporate success. For anyone seeking to navigate their way to operational excellence, Mr. Muenzing is the expert to turn to. With his visionary leadership, profound expertise, and exceptional ability to create lasting improvements, he continues to shape the future of organizations across the globe.
To request further information about Mr. Muenzing through Appleton Greene, please Click Here.
(CLP) Programs
Appleton Greene corporate training programs are all process-driven. They are used as vehicles to implement tangible business processes within clients’ organizations, together with training, support and facilitation during the use of these processes. Corporate training programs are therefore implemented over a sustainable period of time, that is to say, between 1 year (incorporating 12 monthly workshops), and 4 years (incorporating 48 monthly workshops). Your program information guide will specify how long each program takes to complete. Each monthly workshop takes 6 hours to implement and can be undertaken either on the client’s premises, an Appleton Greene serviced office, or online via the internet. This enables clients to implement each part of their business process, before moving onto the next stage of the program and enables employees to plan their study time around their current work commitments. The result is far greater program benefit, over a more sustainable period of time and a significantly improved return on investment.
Appleton Greene uses standard and bespoke corporate training programs as vessels to transfer business process improvement knowledge into the heart of our clients’ organizations. Each individual program focuses upon the implementation of a specific business process, which enables clients to easily quantify their return on investment. There are hundreds of established Appleton Greene corporate training products now available to clients within customer services, e-business, finance, globalization, human resources, information technology, legal, management, marketing and production. It does not matter whether a client’s employees are located within one office, or an unlimited number of international offices, we can still bring them together to learn and implement specific business processes collectively. Our approach to global localization enables us to provide clients with a truly international service with that all important personal touch. Appleton Greene corporate training programs can be provided virtually or locally and they are all unique in that they individually focus upon a specific business function. All (CLP) programs are implemented over a sustainable period of time, usually between 1-4 years, incorporating 12-48 monthly workshops and professional support is consistently provided during this time by qualified learning providers and where appropriate, by Accredited Consultants.
Executive Summary
Unlocking Competitive Advantage with High-Performing Operations
Operational Excellence
Purpose and Principles
Operational Excellence (OpEx) plays a pivotal role in enhancing a business’s competitiveness by elevating efficiency, reducing expenses, enhancing quality, and fostering innovation. By streamlining processes and promptly addressing customer demands, companies gain a significant advantage in the fiercely competitive market. Moreover, OpEx also helps in mitigating risks and fortifying resilience, ensuring sustained success irrespective of whether a company is involved in producing things, handling transactions, or caring about people.
Unleashing the Power of Continuous Improvement
OpEx is more than a buzzword; it’s a philosophy embraced by leading organizations to drive consistency, growth, and sustainability through unwavering commitment to excellence. By integrating sustainable change into their culture and practices, companies achieve operational breakthroughs. Key principles include quality commitment, leadership engagement, employee involvement, seamless teamwork, strategic focus, customer value, agile execution, process excellence, and vision alignment. Embracing these elements unlocks extraordinary short-term results and fosters a sustainable competitive advantage through OpEx.
Teamwork and Culture
Effective teamwork is imperative for operational excellence. Organizations must foster a culture of collaboration, where individuals work synergistically towards common goals. This entails fostering open communication, sharing knowledge, and encouraging cross-functional collaboration. A culture of continuous improvement must permeate the organization, empowering employees to proactively identify opportunities for enhancement and take ownership of their work.
Committed Leadership and Performance Management
Leadership plays a pivotal role in driving operational excellence. Committed leaders provide a clear vision, set high expectations, and lead by example in their dedication to ongoing improvement. They establish robust performance management systems that align individual and team goals with the organization’s overarching objectives. Through regular feedback, coaching, and recognition, leaders inspire employees to strive for excellence and actively contribute to the organization’s success.
Continuous Improvement and Process Excellence
Continuous improvement lies at the heart of operational excellence. Organizations must establish structured methodologies such as Agile Lean Six Sigma (ALSS) to systematically identify and eliminate waste, variability, and complexity, while streamlining processes and drive efficiency. By empowering employees to suggest improvements and providing them with the necessary tools and resources, organizations tap into a valuable wellspring of knowledge and innovation.
Risk and Quality Management
Operational excellence demands an unwavering focus on risk and quality management. Organizations must proactively identify and mitigate potential risks to ensure seamless operations. Quality management practices, including robust standards, quality at the source, stringent controls, regular audits, and a strong customer feedback loop, enable organizations to consistently deliver reliable products and services that meet or exceed customer expectations.
Organizational Structure and Alignment
An effective organizational structure is vital for operational excellence, facilitating clear communication channels, streamlined decision-making processes, and individual accountability. Departments and teams must be aligned to work seamlessly together, breaking down silos and fostering cross-functional collaboration. Furthermore, the organizational structure must be closely aligned with the organization’s vision and mission, ensuring that all efforts contribute cohesively to the overarching strategic goals.
The Four Pillars
Team enablement, strategy deployment, performance management, and process excellence form the bedrock of driving excellence in operations. Team enablement fosters a collaborative culture, inspiring innovation and continuous improvement. Strategy deployment aligns efforts with the overall vision, ensuring goals resonate at every level. Performance management provides feedback and motivation for excellence. Process excellence streamlines operations, minimizing waste, and enhancing customer satisfaction. Together, these pillars empower organizations to excel, adapt, and thrive in today’s competitive landscape.
Embracing Excellence
Wholeheartedly adopting the specific elements of OpEx establishes a robust foundation for long-term success. Operational excellence empowers organizations to streamline processes, provide exceptional value to customers, proactively address risks, and swiftly adapt to evolving market conditions. By striving for excellence, organizations can set themselves apart, foster sustainable growth, and sustain a competitive edge in today’s dynamic business environment. OpEx transcends being a mere buzzword; it is the pathway to lasting success.
Overcoming Barriers
Pursuing OpEx demands a mindset and cultural shift, but not all companies prioritize it, leading to short-term gains at the expense of long-term benefits. Some lack resources or expertise, and others see it as an operational issue rather than a strategic one. Without a clear understanding and commitment to it, companies miss out on opportunities for growth and competitiveness. To take advantage of OpEx, we will now look at its history and its potential to improve business performance in any manufacturing or service operation.
Pioneers and History
The concept of OpEx has many fathers; it evolved over time as organizations have sought to improve their operations and drive greater efficiency and productivity. The history of OpEx can be traced back to the early 20th century when organizations began to focus on standardizing processes to drive greater consistency while reducing waste, variability, and unevenness – the 3 great losses.
Prior to industrialization, craftsmen were responsible for overseeing every aspect of production or service, leading to difficulties such as fluctuating results, inconsistent output, and quality dependent on individual skills, as illustrated by the machine shop example below. However, OpEx revolutionized these practices, enhancing efficiency and reliability across all crafts and industries.
The start of industrialization brought a transformative period in history, shifting from traditional craftsmanship to mechanized production. Key changes included specialized tasks at workstations, enhancing efficiency and productivity. Standardization ensured uniform quality, revolutionizing manufacturing, and paving the way for mass production and the modern industrial era.
One of the pioneers of the OpEx movement was Henry Ford, who implemented the assembly line process in his automobile factory in the early 1900s. This revolutionary process allowed Ford to produce cars more quickly and at a lower cost, ultimately making automobiles more accessible to the public.
During World War II, the Japanese developed the Toyota Production System (TPS) as a response to the scarcity of resources and the need for greater efficiency. The TPS emphasized the elimination of waste, continuous improvement, and a focus on delivering value to customers. This system became the foundation of what is now known as Lean Manufacturing.
In the 1980s, the Total Quality Management (TQM) movement gained popularity in the United States. TQM focused on improving quality by involving all employees in the process, and it also emphasized the importance of customer satisfaction.
In the 1990s, Six Sigma was developed by Motorola to improve quality and reduce defects in manufacturing processes. Six Sigma uses statistical methods to identify and eliminate variations in processes, resulting in greater consistency and quality.
In the early 2000s, the OpEx movement began to shift away from a focus solely on manufacturing and into other areas of business, such as healthcare, banking, education, hospitality, and service industries. This broader approach to OpEx emphasized the importance of process improvement in all aspects of a business, including customer service, finance, and human resources.
Today, virtually all leading companies have made operational excellence part of their strategies for improving agility and productivity. Companies across industries, from manufacturing to healthcare to finance, have adopted OpEx principles to drive continuous improvement and create a culture of excellence.
In conclusion, the history of OpEx is a story of organizations seeking to improve their operations through a variety of methodologies and approaches, which includes Lean, Agile, and Six Sigma. Although the specific methods and tools have evolved over time, the goal of OpEx remains the same: to systematically increase agility, efficiency, productivity, and customer satisfaction by continuously improving processes without limiting itself to the use of a single methodology or toolbox.
Current Position
Operational Excellence (OpEx) has become a well-established management philosophy and strategy that aims to improve business processes and systems. Its popularity has been growing in the last few decades, with many organizations adopting it to enhance their agility, efficiency, productivity, quality, and customer satisfaction.
Today, OpEx is widely used in various industries, including manufacturing, healthcare, finance, and services. Many organizations have made it central to their strategy, and methodologies such as Lean, Agile, Six Sigma, TQM, and CI have become popular frameworks to implement OpEx. The adoption of OpEx has led to significant improvements in businesses, making them more competitive, regardless in which sector or region they operate. Even small companies in emerging markets have successfully deployed OpEx principles in their operation, such as a small food-shop in Mexico is using a bicycle rim to hold customer orders in the sequence they are received and synchronize the restaurant with the kitchen. One turn of the rim means that all customers have been served, which must be kept under five minutes to fulfill the service promise and keep their customers happy.
Despite its numerous benefits, deploying OpEx can be challenging for organizations. One of the significant hurdles is resistance to change. Implementing OpEx requires significant changes to existing processes and systems, which can lead to resistance from employees who are comfortable with the status quo. This challenge can be overcome by involving employees in the deployment process, providing them with the necessary training and support to help them adapt to the new systems and processes. OpEx formalizes processes and highlights problems, but not everyone endorses such transparency – usually only performers do.
Another challenge is the significant investment required in training, technology, and infrastructure. This can be a barrier for organizations operating in firefighting mode, where immediate issues take precedence over long-term investments. However, investing in OpEx can bring significant long-term benefits, including increased productivity, improved quality, and profitability. Therefore, it is always critical to take a longer-term perspective and look not only at the direct cost savings, but also at the increased market potential from increased agility, responding faster to customer needs than competitors do.
Organizations that have successfully implemented OpEx have realized many benefits. For instance, it has improved employee engagement and motivation by empowering employees to identify and solve problems in their work processes. This approach contrasts with a command-and-control style, where employees feel driven and controlled by the system. OpEx has also led to increased operational agility and efficiency, reducing lead times, costs, and increasing revenue, which has ultimately improved the bottom line. From my personal experience, most employees support OpEx once they have experienced how it works, and how it helps them to perform their tasks better and faster.
In conclusion, OpEx is a management philosophy and strategy that has become widely recognized across various industries. While deploying OpEx comes with challenges such as resistance to change and significant investments, the benefits realized by organizations that successfully implement it are numerous. By improving productivity, reducing waste, enhancing quality, and increasing profitability, OpEx helps organizations stay competitive in a rapidly changing global marketplace. It is not surprising that most organizations that adopt OpEx never look back, but rather increase the scope and scale of the program to tackle an even greater part of their value chain, pursuing Business Excellence by additionally including commercial, innovation, finance.
Key Questions
To successfully initiate the OpEx journey, it is helpful to assess the current situation by answering the following 10 key questions:
1. Condition: Is everything in order, and is everyone satisfied with the current state of affairs?
2. Problem: What specific problem needs to be solved, what goal must be achieved, and what gap requires closing?
3. Effects: What benefits will be realized if the problem is solved, and what consequences might arise if it is ignored?
4. Leadership: Has a clear vision been established, indicating where the team should be heading and why?
5. Alignment: Is there a shared unity within the team concerning the direction, purpose, and approach?
6. Resourcing: Are sufficient time, staff, and budget allocated to ensure a successful outcome?
7. Plan: Is there a well-defined roadmap in place, complete with milestones and clear responsibilities?
8. Skills: Are team members adequately trained and capable of effectively executing the program?
9. Incentives: Is there a compelling reason for everyone to actively engage and embrace change?
10. Communication: Are all team members well-informed, enabling them to actively participate and contribute?
The Operational Excellence program will systematically address all 10 points to bring your team and operation to the next level.
Future Outlook
As a business management philosophy and strategy, Operational Excellence (OpEx) aims to continuously improve processes and systems to achieve greater agility, efficiency, productivity, quality, and customer satisfaction. It has been a cornerstone of modern business practices for decades, and its importance is only increasing in today’s hyper-competitive and constantly evolving marketplace. In this article, we will examine the outlook of Operational Excellence and explore its potential impact on businesses and industries.
Digitalization
One of the key trends driving the future of operational excellence is digitalization. The proliferation of digital technologies has transformed the way businesses operate, and OpEx is no exception. With the advent of artificial intelligence, machine learning, data analytics, and the internet of things (IOT), businesses now have unprecedented access to data and insights that can help them optimize their operations. This data-driven approach to OpEx is expected to become even more widespread in the future, as more and more businesses leverage digital tools to gain a competitive advantage. Even small businesses today can take advantage of Digital-OpEx by using free, off-the-shelf tools, such as GoogleSheets, connected to wireless sensors linked to cameras that use intelligent image analysis and pattern recognition to streamline processes and manage performance.
Sustainability
Another trend that is shaping the future of Operational Excellence. As consumers become increasingly concerned about environmental and social issues, businesses are under pressure to operate in a more sustainable and responsible manner. OpEx can help companies achieve this by identifying and eliminating waste, reducing energy consumption, and improving the efficiency of their operations. In the future, we can expect to see a greater emphasis on environmental, social, and governance (ESG) aspects as core components of OpEx.
Adaptation
The rise of agile and flexible work practices is another trend that is likely to impact the future of Operational Excellence. As remote work becomes more common and businesses seek to become more adaptable to changing market conditions, OpEx will need to evolve to accommodate these new ways of working, supporting capacity-resource planning (CRP) and skill-building and load leveling of the workforce. This may involve adopting more Agile and Lean methodologies, and investing in digital tools that facilitate collaboration and remote work.
Technology
The future of operational excellence will be profoundly influenced by an array of ongoing technological advancements. Artificial Intelligence (AI) and Machine Learning (ML) will play a pivotal role by enhancing data analysis, predictive maintenance, and process optimization, enabling data-driven decision-making and streamlined operations. Concurrently, the Internet of Things (IoT) will provide real-time insights into various operational aspects like equipment performance, supply chain logistics, and inventory management, facilitating proactive maintenance and improved productivity. Robotic Process Automation (RPA) will further revolutionize operational excellence by automating repetitive tasks with software robots, reducing errors, and freeing up resources for more strategic activities, resulting in increased efficiency and cost savings. Leveraging Big Data and Analytics will empower companies to optimize operations across various areas, from supply chain management to customer service. Cloud Computing will play a significant role in implementing OpEx initiatives across multiple locations, fostering real-time collaboration, scalability, flexibility, and accessibility. Blockchain technology will enhance transparency and trust in supply chain operations, ensuring the traceability and authenticity of products and transactions. Additionally, Augmented Reality (AR) and Virtual Reality (VR) will be pivotal in employee training, visualizing complex processes, and efficient troubleshooting, thereby fostering faster learning and problem-solving. The emergence of 5G+ Connectivity will support real-time data transmission, facilitating quicker decision-making and remote monitoring of operations. Moreover, the integration of Autonomous Vehicles and Drones will optimize transportation and logistics, leading to reduced delivery times and increased overall efficiency. The concept of Digital Twins, creating virtual replicas of physical assets or processes, will enable simulations, analysis, and optimization without disrupting actual operations. Effectively incorporating these technological advancements into their operations will provide businesses with a competitive edge, fundamentally transforming operational excellence and positioning them for future success.
Conclusion
As we look ahead to the future of operational excellence, it is important to remember that this is not just a buzzword or a passing trend. It is a philosophy that has stood the test of time and has helped countless businesses achieve breakthrough objectives, massive productivity gains, and sustainable success. Whether it is through digitalization, sustainability, technology, or some other means, the future of OpEx is bright, and businesses that embrace this philosophy will be well positioned to thrive in the years to come. The picture below shows a team in Sao Paulo, Brazil, celebrating their journey to become regional OpEx champions. This is a testament to the potential and rewards that await those who use Operational Excellence in their endeavors to drive performance and advance careers.
Curriculum
Operational Excellence – Part 1 – Year 1 – Foundational
- Part 1 Month 1 Program Charter
- Part 1 Month 2 Strategic Alignment
- Part 1 Month 3 Problem Statement
- Part 1 Month 4 Causal Analysis
- Part 1 Month 5 Solution Development
- Part 1 Month 6 Pilot Study
- Part 1 Month 7 Solution Roadmap
- Part 1 Month 8 Capability Building
- Part 1 Month 9 Solution Implementation
- Part 1 Month 10 Solution Standard
- Part 1 Month 11 Impact Assessment
- Part 1 Month 12 Learning Leverage
Operational Excellence – Part 2 – Year 2 – Tactical
- Part 2 Month 1 Process House
- Part 2 Month 2 Target Conditions
- Part 2 Month 3 Digital Twin
- Part 2 Month 4 Lean Application
- Part 2 Month 5 Six Sigma Application
- Part 2 Month 6 Agile Application
- Part 2 Month 7 Portfolio Optimization
- Part 2 Month 8 Workflow Digitalization
- Part 2 Month 9 Digital Standards
- Part 2 Month 10 Target Organization
- Part 2 Month 11 Management System
- Part 2 Month 12 Execution Engine
Operational Excellence – Part 3 – Year 3 – Strategic
- Part 3 Month 1 Strategic Anchor
- Part 3 Month 2 Strategic Planning
- Part 3 Month 3 Strategic Adaptation
- Part 3 Month 4 Experience Design
- Part 3 Month 5 Innovation Strategy
- Part 3 Month 6 Technology Roadmap
- Part 3 Month 7 Resource Allocation
- Part 3 Month 8 Institutional Capabilities
- Part 3 Month 9 Change Leadership
- Part 3 Month 10 Governance Integration
- Part 3 Month 11 Risk Mitigation
- Part 3 Month 12 Corporate Culture
Program Objectives
OpEx Preparation: The 10 key questions to assess readiness.
The following list represents the Key Program Objectives (KPO) for the Appleton Greene Operational Excellence corporate training program. The program is structured into three parts – Foundational, Tactical, Strategic – and conducted over a three-year period. This systematic approach empowers participants to fully grasp the content, implement the principles in real-world scenarios, and seamlessly integrate their newly acquired expertise into their daily operations, leading to tangible and measurable outcomes.
Operational Excellence – Part 1 – Year 1 – Foundational
- Part 1 Month 1 Program Charter – Prepare for a transformative journey toward operational excellence. As with any improvement program, establishing a clear structure is essential to overcoming challenges and effectively capitalizing on opportunities. Without a clearly defined program charter, initiatives can easily lose direction, encounter scope creep and resource cannibalization, lead to misunderstandings, and ultimately fail to achieve their objectives. Recognizing the significance of a solid program charter establishes the foundation for a successful program launch and marks the beginning of our journey. In this inaugural training module, you will gain valuable insights and practical strategies to drive your organization towards operational excellence. Discover the driving force behind pursuing excellence, craft a compelling vision statement, and develop a persuasive business case to secure the necessary support and resources. Build a dynamic core team, establish a precise target timeline, and foster a stimulating environment that encourages collaboration and innovation. Learn effective strategies to overcome barriers and implement an efficient control system to track progress and sustain achievements, while paving the way for performance breakthroughs and a culture of continuous improvement. Upon completion of this inaugural training, you will emerge with a clear understanding of the critical role a charter plays in program success. Armed with the tools and techniques acquired during the workshop, you will confidently create and present a well-crafted program charter to key stakeholders, ensuring alignment and support from the start. By establishing a solid foundation, the program is better equipped to avoid potential pitfalls, mitigate risks, and maintain focus on delivering successful outcomes. Ultimately, the training empowers participants like you to become more effective leaders who can drive initiatives forward, foster collaboration, and inspire teams to achieve extraordinary results.
- Part 1 Month 2 Strategic Alignment – Success in any project depends on aligning stakeholders’ expectations and goals. Stakeholders are individuals or groups that have an interest in the success of the project, such as customers, employees, shareholders, suppliers, and others. It is essential to understand their needs and align them to ensure the project’s success. However, if their needs are not aligned, the project is likely to fail. In this training module, you will learn how to identify the people and organizations that are directly or indirectly affected by the project, have an interest, have the power to influence, or have the authority to make decisions about its direction or outcome. You will identify their needs, which may be tangible items like products or profits or intangible items like trust, respect, and recognition. Clearly understanding the voice of the customer (VOC), voice of the business, (VOB), and voice of the employees (VOE) allows you to establish shared goals. You will align them with the overall strategy, communicate the strategy to key stakeholders, monitor progress and adjust the strategy as needed. Doing so encourages collaboration between different teams so that everyone is working toward the same goals. This strategic alignment ensures that the mission, objectives, and strategies are not conflicting with each other. It helps to ensure that the everyone is working towards the same objectives and resources are being used in the most effective way. Upon completion of this training, you will have the foundation for success by aligning stakeholders to support the project’s mission. You will have the tools and mandates necessary to move the project forward, addressing concerns and questions from individuals critical to success. By applying the techniques learned in this module, you will be able to align stakeholders, understand their needs, and develop strategies to meet them. This will improve communication, promote teamwork, and ensure project success.
- Part 1 Month 3 Problem Statement – Defining the problem to solve is crucial to achieving a successful outcome in any project. However, not everyone may be aware of the issue or recognize that there is even a problem, which can make it difficult to identify and address it. Additionally, some may argue that the problem is external and cannot be resolved internally. To overcome these obstacles and achieve the defined goal, an effective problem statement must be created. In this training module, you will learn how to create a concise and clear problem statement that provides focus, direction, and alignment for all stakeholders involved in the project. This statement includes the problem’s context, why it needs to be addressed, specific objectives, the approach to solving it, the impact of the solution on stakeholders, and how to evaluate success. The process begins with identifying the success metric, a quantifiable measure of progress towards the desired outcome. It is essential to select the right key performance indicator (KPI) for the project based on stakeholders’ needs and expectations. This can reveal potential conflicts that must be resolved to solidify the problem statement. Once the success metric is defined and aligned, you will establish the baseline and the performance gap. The baseline is the reference point at the start of the project to measure progress against, while the performance gap is the difference between the baseline and the expected result. Upon completion of this training, you will have identified the gap between the current state and the desired state, providing direction for solution development in the upcoming modules. You will have a clear understanding of which single problem needs to be solved, why, and how to measure success. The problem statement will also serve as a guide to ensure that all stakeholders remain focused on the same goal.
- Part 1 Month 4 Causal Analysis – Identifying the root cause of a problem is essential for effective problem-solving, yet stakeholders often struggle to comprehend the underlying reasons for an issue or have conflicting views on how to address it. Nonetheless, in science and business, it is commonly acknowledged that there is a cause for everything that occurs. By pinpointing the root cause of a problem, we can systematically address it and leverage opportunities for improvement. In this training module, you will learn how to identify the relationships between various variables in the system under investigation. By adopting a comprehensive approach to problem-solving, you will identify the underlying causes of problems, which is a prerequisite for developing effective solutions. Mapping the causal relationships between conditions, actions, and effects is one of the key tools for identifying root causes. This process facilitates understanding why certain outcomes occur and how different factors influence them. Creating a logic-tree that traces back from the symptoms to the root cause of the problem will provide insights into developing strategies for improving performance and preventing future issues. Causal analysis is a critical tool for decision-making as it allows the analysis of both qualitative and quantitative data. Understanding the relationships between different variables in the operating system provides a more holistic understanding of the problem, enabling informed decisions about how to address it. Upon completion of this training, you will have a firm grasp of the direct causes, contributing causes, and root causes of the problem. With this knowledge, you can develop effective solutions that eliminate the root causes of defects, deviations, delays, and disconnects. Ultimately, this leads to improved products and services that are delivered efficiently, resulting in higher customer satisfaction and improved business performance. The ability to identify root causes is a valuable skill for all stakeholders, enabling them to solve problems effectively and capitalize on opportunities for improvement.
- Part 1 Month 5 Solution Development – Despite identifying the root causes of the problem, finding a suitable solution remains elusive. To overcome this challenge, it is essential to prioritize appropriate countermeasures while considering operational and business constraints. Critical factors such as time, costs, people resources, and implementation difficulty must be evaluated to develop practical solutions for each identified cause. Focus must be on solutions that offer the greatest value and effectiveness for all stakeholders. Assessing the probability of success, risk of unintended consequences, stability of the solution over time, and feasibility of implementation based on practical considerations such as timeline, costs, and return on investment is essential to track progress and create impact. In this training module, you will learn how to overcome critical issues, how to identify and prioritize appropriate countermeasures while taking into consideration operational and business constraints. You will also learn to develop practical solutions for each identified cause, assessing the probability of success, risk of unintended consequences, and feasibility of implementation. Additionally, you will develop lead indicators at the operational level to track progress and lag indicators to measure impact. Monitoring lagging indicators at the financial level will help you gauge the effectiveness of your solutions and make any necessary adjustments. Upon completion of this training, you will have a solid solution plan that effectively eliminates the problem or significantly reduces the performance gap. This solution plan is fully actionable and can be executed by the implementation team, addressing the identified barriers effectively. It meets the goals and objectives of all stakeholders while ensuring safety and soundness without causing any harm or other negative consequences. The solution plan is comprehensive, leaving no room for excuses or escapes, and is ready for implementation. To ensure accountability, success measures are firmly integrated into the project scorecard.
- Part 1 Month 6 Pilot Study – To address performance gaps, numerous solution concepts have been developed. However, the effectiveness of these solutions has not been tested in real-life scenarios, leaving doubts about whether they would work under actual operating conditions. Therefore, the aim of this module is to address potential weaknesses of these solution concepts by testing them before implementing them on a larger scale. In this training module, you will learn how to perform a pilot study that tests the feasibility and effectiveness of potential solutions on a smaller scale in a controlled environment. A pilot study involves a limited sample size and resources, with the goal of identifying potential issues that may arise during a full-scale rollout. The process includes selecting a representative group of people and equipment, designing the study, developing a plan for the pilot, and defining the methods and materials to be used. The data collected is then analyzed to draw conclusions from the pilot study. If necessary, the solution concept is adjusted based on the results, and the study is repeated. Upon completion of this training, you will have validated the solution concept at a pilot-scale in a controlled environment and tested its effectiveness under actual operating conditions by carefully introducing constraints and variability. Through several iterations, the solution will be optimized until it is fully qualified, ensuring its successful implementation in the actual operating environment. By learning how to test the feasibility and effectiveness of solutions before implementing them on a larger scale, you will save time and resources, while also mitigating risks.
- Part 1 Month 7 Solution Roadmap – A well-defined plan is a crucial component of successful change management, strategy deployment, and project execution. Merely having a clear destination and committed crew is not enough to implement a solution. To navigate unfamiliar terrain, overcome obstacles, and accomplish the mission, a detailed roadmap is required. In this training module, you will learn how to develop a master plan that outlines the goal, milestones, success measures, and the most effective path to achieve the desired outcome. This roadmap is an essential communication tool that helps articulate what needs to change, why it needs to change, and the order in which changes should be made. It aligns the organization’s functions and activities vertically and horizontally with its project objectives. The roadmap specifies tasks, deliverables, timelines, responsibilities, and measures. Without such a solid plan, there will be false starts and constant course corrections, making it challenging to achieve real progress. Upon completion of this training, you will have a detailed implementation roadmap that makes the vision actionable and tangible. It considers the organization holistically, ensuring that all areas of change are well understood and adequately covered. Capability-based planning helps team members understand existing capabilities, the changes required to achieve the objective, and their priority. The resulting roadmap not only outlines how goals will be achieved, but it also specifies who is responsible, when resources are required, and for how long. It includes specific milestones and deliverables, making progress measurable and allowing for early identification of problems and corrections to keep the project on track.
- Part 1 Month 8 Capability Building – The introduction of new technologies or methods usually requires people to acquire new skills and capabilities. Without these essential abilities, anxiety and fear can take hold, leading to paralysis and an inability to adapt. To effectively manage change, it is important to identify which skills and capabilities are critical, which ones are already present, and which need to be developed. Moreover, motivating people to learn these new skills is key to project success and sustainability. In this training module, you will learn how to identify skill gaps and develop training plans to close them. The objective is to equip team members with the cognitive, socio-emotional, and technical skills required to implement the change and perform in the new way. Training plans need to address the mindset barrier of “I don’t know how” so that those involved in the transition can successfully think and work in the new way. This involves developing cognitive skills to understand complex ideas, perform advanced data analysis, solve complex problems, design and control technology. Additionally, socio-emotional skills are required to navigate interpersonal and social situations effectively, including leadership, teamwork, self-control, and grit. Technical skills, knowledge, expertise, and interactions must be considered to perform required tasks, including mastery of required materials, tools, and technologies. Along with developing training plans, it is important to identify motivators and create incentives for individuals to learn these skills. People are primarily motivated by two forces – gaining pleasure and avoiding pain. Therefore, individuals must perceive and receive benefits from the change to be willing to engage and learn new skills. If they do not see the value in the change, they are likely to resist implementing new processes. Upon completion of this training, you will have identified the skills and capabilities required from team members to perform effectively in the new structure and system. Skill matrices and effective training plans will have been developed and deployed, and incentives created to keep individuals motivated during the upskilling process until qualification is achieved. These steps are crucial preconditions for successfully execution of the roadmap.
- Part 1 Month 9 Solution Implementation – Implementing the new solution can involve introducing a new technology, restructuring an organization, streamlining workflows, or changing how people work. When the concept is already proven, a detailed plan is in place and people are trained to execute this plan, then it is crucial to ensure effective execution in an agile way to achieve success at full scope and scale. In this training module, you will learn how to implement a solution effectively, establish transparency and communicate clearly to ensure that all stakeholders are aware of the tasks, timeline, and any changes. Assigning clear roles and responsibilities helps ensure that everyone involved understands what is expected of them. Monitoring progress against the plan is necessary to identify any issues or roadblocks and make necessary adjustments to stay on track. You will also ensure access to necessary resources, such as equipment, software, and personnel, which is essential to successful implementation. Additionally, you will celebrate successes and encourage the team to learn from failures. This approach helps to keep the team motivated and focused on the goal while learning from setbacks. Establishing feedback loops allows for continuous improvement, gathering feedback from stakeholders and end-users helps to identify areas for change and ensure the implementation is meeting its intended purpose. Upon completion of this training, you will have developed the skills and capabilities for successful project execution. You will be capable to effectively execute the roadmap and realize desired outcomes. Communication, role clarity, resource availability, progress monitoring, celebration of successes, learning from failures, and positive feedback loops are essential for successful implementation. By following these key steps, you will guide the target organization to execute the solution effectively and achieve the intended outcomes.
- Part 1 Month 10 Solution Standard – After successfully implementing the solution, it is crucial to ensure that it remains effective over time. This is where standardization comes in. Standardization involves creating a consistent set of guidelines and procedures to embed the new structure, method, or system in the organization. Without standardization, there is a high risk that processes will deteriorate, variability will increase, performance will decline, and customer satisfaction over time. Therefore, standardization is essential to achieve sustainable success. In this training module, you will learn how to standardize the new way of working. You will follow a structured approach to identify the key areas where variability is high, and standardization is required to mitigate risk. This involves identifying the steps and workflows that are essential to achieve the desired outcomes. Once you have identified the areas that need standardization, you will learn how to develop standard procedures and instructions that are simple, clear, and concise. These instructions will provide guidance on how to perform the task, by whom, when, and how, including the tools, equipment, materials, and authority required. You will also learn how to embed these new procedures into existing structures and how to incorporate them into the regular review cycle to ensure they remain current and relevant. Upon completion of this training, you will have standardized and embedded the solution in the target organization. This standardization will result in improved quality, reduced variability, improved communication, and increased efficiency through this new structure, system, or procedure. Standardization lays the foundation for continuous improvement, making it easier to identify areas for improvement and make changes to the process. By achieving greater levels of consistency and efficiency, you will have improved customer satisfaction and overall performance levels. Standardization ensures that the output of the new process remains consistent, regardless of who performs the task or where it is performed. This consistency is important in achieving and maintaining high levels of customer satisfaction, leading to increased loyalty and growth.
- Part 1 Month 11 Impact Assessment – During and especially after implementing the solution, it is essential to assess its impact to determine whether it is delivering the intended benefits. Project impact assessment involves evaluating the effect of the project on the organization, stakeholders, and the environment. It helps to identify the strengths and weaknesses of the project and enables the team to make necessary adjustments to ensure that the desired outcome is achieved. In this training module, you will learn how to assess progress and impact on the operational and financial level. This process starts by analyzing key indicators from the scorecard, measuring the performance of the project during the deployment phase. These are quantifiable measures that evaluate the success of the project and are used to determine whether its objectives have been achieved. You will learn to use lead indicators to identify potential risks post implementation and lag indicators to project benefits for the next accounting period. Both types of indicators are required to assess progress and impact of the project. For the business case, financial benefits are an important aspect to evaluate success. This involves assessing the financial costs and benefits of the project, including the return on investment (ROI) and net present value (NPV). The business case for the project must be evaluated to ensure that it is delivering the desired financial benefits, and that the investment in the project was justified. Upon completion of this training, you will have established an impact assessment framework, defined the criteria for measuring success, analyzed scorecard data, and projected the financial impact over the accounting period following implementation, which is typically 12 months. The project’s business case will be updated to reflect implemented results and also expected benefits for the next accounting period.
- Part 1 Month 12 Learning Leverage – After successfully completing the project, it may be tempting to move on to the next task without looking back. However, this approach is inefficient because valuable lessons learned during the project could be applied to solve future challenges or problems more effectively. This is why it is essential to practice Yokoten, a Japanese term for “horizontal deployment” or “sharing”. It involves extracting and spreading best practices, knowledge, and ideas from the project across different areas of an organization to systematically drive continuous improvement. In this training module, you will learn how to practice Yokoten by identifying the key success factors of the project and documenting them, which includes the solutions implemented, challenges faced and instructions on how to overcome them. This document will then be used to educate people who will be implementing the same process in a new area. It will not only focus on technical aspects but also encourage collaboration and sharing of ideas among team members. Once the process is scheduled for implementation in a new area, you will define ways to monitor and measure its effectiveness to ensure continuous improvement. Upon completion of this training, you will have enabled your organization to reduce duplication of effort, improve quality and consistency, and create a culture of continuous improvement. By sharing best practices, teams learn from each other, improve efficiency, and achieve greater success together. The organization leverages learning by increasing scope and scale, identifying areas that could benefit from applying the lessons to a new project, establishing a new improvement or innovation team, documenting and sharing successful ideas from the current project, providing adequate training, and monitoring the effectiveness of new processes. By doing so, organizations can achieve improved efficiency and ultimately drive greater success.
Operational Excellence – Part 2 – Year 2 – Tactical
- Part 2 Month 1 Process House – Weather we realize it or not, everything we do is a process, and we all play part of many processes. The process house represents a holistic approach aimed at identifying core processes, support processes, and critical interfaces within an organization to optimize and streamline these processes to deliver maximum value to customers while enhancing efficiency and productivity. Failing to understand how processes interact leads to delays, breakdowns, inefficiencies, stonewalling, and unhappy customers. Take, for example, a manufacturing company that fails to define its processes and interfaces. Such a company is likely to face challenges in managing its supply chain efficiently, leading to delays in sourcing materials, poorly organized warehousing, and increased logistics costs. Additionally, there might be a lack of collaboration between departments, leading to a disconnect between engineering, research, and development practices, hindering innovation and improvement in their products. Customer-centric strategies may be undermined, causing reduced customer loyalty and negatively impacting sales and marketing efforts. In this workshop, you will learn how to identify core processes, support processes, and critical interfaces within your organization. You will explore methods to optimize value streams and enhance supply chain management, product lifecycle management, operations, customer relationship management, human resources, finance and controlling, information technology, quality management, process interface alignment, performance metrics monitoring, continuous improvement practices, and cross-functional collaboration. Upon completion of this training, you will be equipped with the knowledge and tools to identify and optimize core processes, enhance support processes, and align critical interfaces, leading to improved collaboration and smooth information flow.
- Part 2 Month 2 Target Conditions – They are specific future states that organizations aim to achieve through problem-solving and continuous improvement efforts. Unlike common goal setting, target conditions focus on critical processes and interfaces, providing a clear and concise definition of the desired state to be achieved, while driving effective problem-solving by providing a tangible destination for improvement efforts. Without defining these target states, the lack of clarity leads to ambiguous goals, making it challenging to measure progress accurately, leading to misalignment among team members and stakeholders, wasted time and resources, while struggling to prioritize improvement efforts, hindering the success of their initiatives. In this workshop, you will learn about the importance of clear and concise definition, enabling you to communicate target conditions effectively to teams and stakeholders. You will also gain insight into visualizing and comparing the target condition with the current state and desired future state, enhancing your understanding of the improvement journey, while considering resources, constraints, and stakeholders’ expectations. Upon completion of this training, you will have acquired the skills and knowledge to define clear and measurable target conditions. You will be adept at communicating the importance of such conditions and leveraging effective communication techniques to engage your teams and stakeholders. By integrating data-driven analysis into your decision-making processes, you will be able to assess the feasibility of your target conditions and mitigate potential risks. You will be equipped with problem-solving tools and methodologies, fostering a sense of ownership, urgency, and motivation among team members. Organizations, in turn, will benefit from increased efficiency, improved processes, and a culture of continuous improvement, ultimately driving greater success and achieving their strategic objectives.
- Part 2 Month 3 Digital Twins – They are virtual models to simulate real-world systems, enabling us to optimize processes, test improvement concepts, and make data-driven decisions. They will revolutionize our reality. Without such model, we miss out on a transformative tool that can significantly enhance our operational efficiency. For example, consider a manufacturing facility with a virtual model that mirrors the actual production line, allowing the team to simulate various scenarios and evaluate potential changes before implementing them in the real operational environment. This approach helps in identifying bottlenecks, optimizing resource allocation, and refining improvement concepts, leading to reduced downtime, increased throughput, and overall enhanced performance. In the workshop, you will gain comprehensive insights about digital twinning, starting with knowledge sharing to educate stakeholders about the concept’s significance. You will learn how to conduct a value identification assessment to recognize the specific benefits that a digital twin can bring to our operations. Additionally, the workshop will delve into data gathering, validation processes, and software evaluation, equipping you to develop a reliable and accurate twin. Integration planning will ensure a seamless merge with existing systems and processes, facilitating smooth data flow and interoperability. To address potential challenges, the workshop will include risk assessment and case study analysis, providing practical understanding and best practices for digital twinning. You will also learn how to leverage the digital twin for simulation modeling, defining performance metrics, identifying bottlenecks, and determining optimal update frequencies and detail levels. Upon completion of this training, you will possess the expertise to develop and maintain a digital model, enabling you to drive continuous improvement efforts within our operations.
- Part 2 Month 4 Lean Application – Lean is key to business survival, aimed at streamlining and standardizing processes to achieve complete, accurate, and timely output, by eliminating wastes, such as slack, excess, and defects. Lean, Agile, Six Sigma – so many approaches – what’s the difference? Lean focuses on streamlining and standardizing processes to eliminate wastes, while Agile emphasizes iterative and adaptive development, and Six Sigma aims at reducing defects and process variations through data-driven approaches. Without driving Lean, organizations experience inefficiency, increased costs, reduced customer satisfaction, and missed deadlines. This might not be a problem if you are operating as a monopoly. But most companies must be efficient to compete. To illustrate, let’s consider a manufacturing company that decides to apply Lean to production. Through careful analysis and process mapping, they identify bottlenecks, excessive inventory, and unnecessary transportation steps. By implementing flow, balancing workloads, and introducing pull systems, the company optimizes the process, resulting in reduced lead times, improved productivity, and better utilization of resources. In this workshop, participants will learn practical approaches to implementing Lean within their processes. Starting with identifying the target process, attendees will gain insights into understanding customer demand, creating detailed process maps, and conducting waste analysis. The workshop will focus on redesigning processes to establish smooth flow, synchronizing work with actual demand or planned schedule, and implementing pull systems and leveling procedures to ensure efficient operations. Creating standard work instructions, providing employee training, and utilizing visual management techniques foster a culture of continuous improvement. Upon completion of this training, participants will possess the knowledge and tools to optimize processes, leading to significantly reduced waste, increased productivity, and enhanced customer satisfaction.
- Part 2 Month 5 Six Sigma – That’s 99.99966% perfection or 3.4 problems in one million transactions. Six Sigma encompasses more than just quality levels, it’s about boosting capability for consistent, reliable, and efficient output, while reducing defects and enhancing overall performance. Neglecting Six Sigma principles often leads to uncontrolled variability, increased defect and error rates, operational inefficiencies, dissatisfied customers, and reduced competitiveness. For example, a company that ignores process variability may face quality issues, resulting in defects and inconsistencies, leading to customer complaints and loss of trust, ultimately affecting sales and revenue. The absence of data-driven decision-making and standardization further hampers the identification and resolution of underlying process issues. In this workshop, you will learn basic tools and methodologies to practically apply Six Sigma in your area, use SIPOC (Suppliers, Inputs, Process, Outputs, Customers), a high-level process mapping tool to provide an overview of a process and its key elements. You’ll further explore data analysis techniques to identify patterns affecting process capability and use process mapping to detect bottlenecks and improvement opportunities. You’ll employ Statistical Process Control (SPC) techniques for process monitoring and deviation detection. The workshop will also focus on skill development through problem-solving and statistical analysis training, empowering you and your team to address challenges effectively. By promoting cross-functional collaboration and integrating customer feedback, you’ll align the process with customer needs, enhancing overall satisfaction. Identifying automation opportunities and benchmarking against industry best practices further optimize process capability. Upon completion of this training, you will have the expertise to apply Six Sigma principles in your area for reliable and consistent output. Improved data analysis skills will lead to better decision-making, reducing defects and increasing efficiency. Continuous monitoring and review will sustain and build on improvements, benefiting your organization with enhanced customer satisfaction, competitiveness, and overall performance.
- Part 2 Month 6 Agile Application – Agile has revolutionized project management, leaving traditional methods behind. It aims to nurture an adaptive mindset, emphasizing collaboration and continuous learning. This fosters effective responses to changing priorities, customer feedback, and market demands, leading to increased efficiency and productivity. Without an agile mindset, teams struggle in dynamic work environments, causing rigid and inefficient processes. The absence of iterative and adaptive planning leads to projects exceeding schedules and budgets, with little room for adjustments. Lack of cross-functional teams and customer involvement results in siloed work and poor understanding of customer needs, affecting product quality. This workshop covers crucial aspects of Agile in OpEx. Participants will grasp the Agile mindset, stressing adaptability, collaboration, and continuous improvement. Topics include iterative planning, adaptive planning, and the significance of cross-functional teams in boosting efficiency. Involving customers and stakeholders throughout the process fosters transparency and product alignment. Additionally, the workshop implements Agile metrics for data-driven decisions on team performance and process efficiency. Participants will understand the value of daily stand-up meetings, sprint retrospectives, user stories, Kanban boards, timeboxing, feedback loops, and visual management, fostering communication and teamwork. After this training, participants will hold a comprehensive understanding of Agile principles tailored to OpEx. They will be equipped to instill an agile mindset, promoting adaptability and collaboration in their teams and organizations. The application of Agile methodologies will lead to increased productivity, better process efficiency, and a customer-centric approach, benefiting individuals and the organization as a whole. Agile is the way forward, leaving behind outdated traditional methods in project management.
- Part 2 Month 7 Portfolio Optimization – Businesses that streamlined their offerings experienced a 15% increase in profitability. Portfolio optimization involves strategically streamlining a company’s product and service offerings to maximize effectiveness. This process capitalizes on high-performing elements while eliminating low-performing ones, preventing reduced profitability, inefficient resource allocation, missed market opportunities, and loss of competitiveness. Imagine a fictional consumer electronics company with a wide range of products and services in its portfolio. Some are highly profitable and in demand, while others have dwindling sales and little customer value. Without portfolio optimization, the company might continue investing in less profitable products, reducing overall profitability. Additionally, without customer segmentation and market trend analysis, offerings may not align with changing consumer preferences, leading to potential market share loss to more adaptive competitors. This workshop provides a practical approach to portfolio optimization, covering key elements such as portfolio analysis, customer segmentation, market trend analysis, risk-return assessment, and product-service rationalization. Upon completion, participants will understand portfolio optimization’s vital role in operational excellence. They will gain practical tools to streamline their organization’s offerings, align with customer needs and market trends, and enhance profitability and competitiveness. The benefits extend to the entire team or organization, enabling informed decisions, efficient resource allocation, seizing market opportunities, and adapting proactively to changing dynamics for sustained success and growth.
- Part 2 Month 8 Workflow Digitalization – “Go digital or go obsolete” has never been more relevant. Workflow digitalization is crucial for modern businesses aiming to enhance operational performance through technology. It involves optimizing, automating, and streamlining processes to create an efficient and transparent workflow ecosystem, driving productivity and informed decision-making. Neglecting digitalization comes with severe consequences, including manual errors, slow processes, lack of real-time insights, decreased collaboration, and compromised data security. This impacts overall productivity and competitiveness. For instance, a manufacturing company relying on paper-based supply chain management faces delays in order processing, inventory tracking issues, and an inability to adapt to market demands, leading to bottlenecks and customer dissatisfaction. To address these challenges, a workshop offers practical tools and methodologies. Data analytics extracts meaningful insights, enabling data-driven decision-making and process optimization. Robotic automation delegates repetitive tasks to software robots, freeing human resources for strategic tasks. Cloud integration facilitates seamless collaboration and knowledge-sharing among teams. Workflow mapping identifies inefficiencies, while real-time monitoring tracks progress and performance metrics transparently. Digital collaboration tools foster communication and productivity, and gamification elements motivate employees to drive engagement. Implementing a digital feedback loop encourages continuous improvement and innovation. Virtual collaboration spaces cater to remote teams, ensuring efficient teamwork despite geographical barriers. In conclusion, embracing workflow digitalization empowers businesses to stay agile, competitive, and prepared for the future. By leveraging technology to its fullest potential, organizations can achieve sustained performance gains and thrive in the dynamic business landscape.
- Part 2 Month 9 Digital Standards – They are encompassing digitized Standard Operating Procedures (SOP) and Standard Work Instructions (SWI), are crucial for achieving process excellence, ensuring consistency, quality, and efficiency in task execution. For instance, in the medical field, the implementation of video procedures has revolutionized the way surgeons transfer their knowledge and experiences to improve the success rate of medical treatments. By digitizing surgical techniques and creating interactive “how-to” video instructions, experienced surgeons can share their expertise with their peers and aspiring medical professionals. These videos offer a detailed and visual understanding of complex procedures, allowing for better comprehension and learning. Younger surgeons can access these video instructions on their digital devices, review them repeatedly, and learn at their own pace. The accessibility and repeatability of video instructions contribute to skill development and competency enhancement, ultimately leading to improved surgical outcomes and patient care. Additionally, video procedures enable surgical teams to collaborate more effectively during critical procedures, ensuring that everyone is aligned with the best practices and standardized processes. This sharing of knowledge and experiences through digital means not only enhances the success rate of medical treatments but also promotes a culture of continuous learning and improvement within the medical community. In the workshop, participants will learn how to create e-instructions, develop user-friendly electronic procedures, implement version control, integrate performance metrics, and encourage cross-functional collaboration, among other topics. They will also gain insights into how digital standards can transform knowledge sharing and skill development, particularly in specialized fields like science, engineering, and management. Upon completion of this training, participants will have the knowledge and tools to enhance user experience, improve process consistency, increase efficiency, and achieve process excellence. The organization will benefit from standardized and updated procedures, reduced errors, improved productivity, and a more agile workflow, ultimately leading to increased overall performance. Moreover, in the medical field, the adoption of digital standards and video procedures will contribute to better outcomes at greater consistency and safety.
- Part 2 Month 10 Target Organization – Companies with well-structured target organizations see up to 30% higher employee engagement and productivity. The key lies in developing a robust framework that ensures capable, empowered, and accountable individuals within the organization, aligned with its vision and goals. A target organization fosters a culture of leadership, empowering employees to take charge and contribute effectively. Without such a structure, inefficiencies, misaligned efforts, and reduced employee morale can arise, hindering long-term success. For example, a financial institution seeking service efficiency and customer satisfaction may suffer from unclear roles and a lack of accountability, resulting in reduced employee productivity and hindrance to growth. In this workshop, participants will learn essential components of a target organization. Leadership development will be emphasized, nurturing capable leaders at all levels. An empowerment framework will be explored to delegate authority and decision-making, fostering ownership and empowerment. Ongoing skill enhancement through training and development will bolster individual capabilities. An accountability matrix will clarify roles and responsibilities, instilling a culture of responsibility. Performance metrics will measure individual contributions, promoting continuous improvement. Talent acquisition strategies will attract skilled individuals aligned with the organization’s vision. Mentorship programs and succession plans will foster knowledge transfer and groom future leaders. Completion of this training equips participants to develop and implement a target organization for OpEx objectives. Capable leaders, empowered individuals, and accountability will be cultivated, benefiting the entire organization. A well-structured target organization will lead to enhanced productivity, streamlined operations, and sustained competitive advantage, enabling success amidst evolving business challenges and opportunities.
- Part 2 Month 11 Tactical Scorecard – They contribute significantly to top-performing companies’ success, accounting for 45% of their achievements. These scorecards play a crucial role in operational excellence by fostering transparency and alignment within organizations. They establish a comprehensive framework of leading metrics and tactics, enabling progress tracking and goal alignment. Without an efficient tactical scorecard, companies face challenges in identifying constraints and focusing on key performance drivers. For instance, a service-based company aiming to improve customer satisfaction may miss out on crucial leading metrics that directly impact customer experience, leading to missed opportunities for improvement. This lack of focus results in stagnant customer satisfaction levels and an inability to address root causes of complaints, ultimately impacting long-term success and customer retention. To address these issues, a workshop offers essential tactics for building an effective tactical scorecard that prioritizes leading metrics. Clear, measurable performance indicators are emphasized to influence operational success positively. Tactics like stakeholder mapping, data integration, and feedback loops are explored to ensure accurate measurement and goal-oriented decision-making. The workshop also covers continuous improvement processes, including regular performance reviews, root cause analysis, and benchmarking against industry best practices. Participants learn to implement real-time reporting mechanisms to swiftly make course corrections when leading metrics deviate from expected outcomes. Upon completing the training, participants gain a comprehensive understanding of constructing a tactical scorecard. They become equipped to drive significant operational improvements, achieve strategic objectives, and proactively respond to challenges. The organization benefits from insights to reengineer products and processes for better performance and a stronger market position. With a well-executed tactical scorecard, companies can navigate the dynamic business landscape with confidence, securing sustained success.
- Part 2 Month 12 Execution Engine – In essence, is a turbocharged management system to achieve automatic excellence. It integrates various strategies, including establishing a learning loop for continuous feedback, designing and integrating performance metrics aligned with strategic objectives, cultivating a culture of experimentation and iteration, and implementing mechanisms to promote knowledge flow and collaboration across departments. Customer focus, stakeholder engagement, resilient design, and data-driven decision-making are also integral components. Missing the execution engine means reinventing the wheel every time. For example, imagine a manufacturing company that lacks an execution engine. They struggle with outdated processes, low employee engagement, and limited collaboration between departments. They receive customer complaints about product quality and slow delivery times, leading to decreased customer satisfaction and ultimately a decline in sales. Without a systematic approach to continuous improvement and data-driven decision-making, the company fails to address these issues effectively, resulting in a significant loss of market share to competitors. In this workshop, you will learn how to build and implement an execution engine to enhance performance. The workshop covers strategies such as learning loops, integrated performance metrics, a culture of experimentation and knowledge sharing, and customer-centric decision-making. You will also gain insights into resilient design, data-driven decision-making, and fostering an innovation ecosystem within your area of responsibility. Upon completion of this training, you will have the tools and knowledge to develop and implement a robust OpEx execution engine. The systematic approach to automatic excellence will result in increased customer satisfaction, higher employee engagement, and better overall performance – through a robust system.
Operational Excellence – Part 3 – Year 3 – Strategic
- Part 3 Month 1 Strategic Anchor – It serves as a guiding star for transformation program programs. It involves conducting a comprehensive competitive analysis to pinpoint the strategic pillar that sets the organization apart from its competitors. By understanding the strengths and weaknesses of competitors, opportunities for gaining a competitive edge are identified. This strategic anchor is essential for positioning the organization effectively within the market, attracting target customers and stakeholders through a unique value proposition. Without a clear guiding anchor, organizations risk drifting aimlessly in a crowded market, struggling to establish their distinctiveness. This lack of direction can lead to reduced customer interest and stakeholder support, affecting the organization’s growth and success. The significance of a well-defined strategic anchor extends to teams and departments seeking funding and executive backing for their initiatives. Without it, there is a risk of inefficient resource allocation, diverting focus away from strategic priorities. In the workshop, participants will gain valuable insights and essential tools to address the key components of the strategic anchor. The training includes conducting a thorough competitive analysis, understanding market positioning, customer segmentation, and performing a SWOT analysis to guide the anchor’s development. Furthermore, attendees will learn the importance of monitoring industry trends, establishing relevant benchmarks, assessing risks, gathering customer feedback, and evaluating suppliers and emerging technologies. Upon completion of this training, participants will possess a clear understanding of anchoring their organizations, aligning them with their strengths and opportunities. By leveraging insights from the analysis, teams and organizations can attract the right target customers and stakeholders, secure funding and executive support for their programs. Additionally, equipped with this knowledge, organizations can optimize resource allocation and adapt swiftly to changing regulatory and market conditions, ensuring the long-term viability and sustainability of their strategic anchor.
- Part 3 Month 2 Strategic Planning – It is essential for organizations to formalize their strategy and ensure sustainability. ESG-driven companies often outperform peers, and investors prioritize sustainable investments. Over 40 countries have supportive ESG regulations, and there are over 500 dedicated ESG funds globally, with ESG companies showing 20% higher financial performance. Consumers overwhelmingly prefer socially responsible companies, and ESG practices can reduce borrowing costs by 15%. The sustainability aspect of strategic planning involves Corporate Social Responsibility (CSR) and Environmental, Social, and Governance (ESG) factors. Without integrating sustainability principles, an organization may miss areas for improvement in its environmental footprint, leading to inefficiencies and lost resource conservation opportunities. Neglecting stakeholder engagement can result in a lack of diverse perspectives, leading to a lack of support for the strategic plan among employees, customers, suppliers, and communities. In this workshop, participants learn a comprehensive approach to strategic planning with a sustainability focus. They integrate CSR and ESG factors, ensuring long-term viability. Topics covered include environmental and social impact assessments, ethical decision-making frameworks, scenario analysis, benchmarking best practices, and sustainability reporting mechanisms. Participants also explore partnerships with like-minded organizations, circular economy principles, inclusivity, sustainability-related risk management, and responsible supply chain practices. After the training, participants gain the tools to lead their organizations in developing sustainable strategic plans. They can identify opportunities for environmental and social improvements, set ethical guidelines, anticipate challenges, and benchmark best practices. This fosters resilience, innovation, competitiveness, and a positive reputation with stakeholders. Embedding sustainability into strategic planning contributes to long-term success and positive impact, creating a more responsible business environment.
- Part 3 Month 3 Strategic Adaptation – Evolve or vanish. Strategic adaptation involves enhancing the business model to boost flexibility, adaptability, performance, and resilience in a dynamic operating environment. Its purpose is to enable organizations to proactively respond to disruptions, uncertainties, and changing customer needs, both internal and external, ensuring sustainable growth and a competitive advantage. Failing to implement strategic adaptation leads to missed opportunities, reduced market competitiveness, and an inability to effectively address emerging challenges. Without strategic renewal, businesses may find themselves trapped in outdated practices, unable to pivot or capitalize on market shifts, ultimately risking stagnation and eventual obsolescence. Let’s consider a retail company that failed to renew its strategy. As customer preferences shifted towards online shopping and contactless experiences, the company stuck to traditional brick-and-mortar stores and resisted integrating digital solutions and customer-centric strategies. Consequently, the company struggled to keep up with competitors, lost market share, and faced financial difficulties. This workshop provides participants with a comprehensive set of strategies and practices to foster strategic adaptation. They will explore collaborative partnerships to leverage knowledge and resources, engage in scenario planning to anticipate disruptions, and embrace customer co-creation for innovative products. The workshop also covers essential concepts such as rapid prototyping, cross-functional teams, decentralized decision-making, and adaptive performance metrics. Armed with this knowledge, participants will be equipped to drive strategic adaptation effectively. They will proactively respond to market shifts and navigate uncertainties to stay ahead of competitors, fostering sustainable growth and increased relevance. Ultimately, embracing strategic adaptation will ensure a thriving and resilient future for both the participants and their organizations, enhancing adaptability, improving performance, and cultivating a workforce capable of tackling challenges with confidence.
- Part 3 Month 4 Experience Design – Companies that prioritize customer experience design outperform others by nearly 80% (McKinsey & Company). This approach revolves around creating a customer-centric strategy and delivering a seamless journey. When neglected, both internal and external customers may become dissatisfied, leading to reduced loyalty, a tarnished brand reputation, and a decline in revenue and executive support. Imagine a retail company that fails to design a user-friendly and personalized online shopping platform. Customers face navigation challenges, receive irrelevant product recommendations, and feel frustrated during checkout. Consequently, they abandon their purchases and turn to competitors with better-designed platforms. In this workshop, you’ll learn a comprehensive approach to customer experience design, encompassing various design-thinking principles. Starting with detailed customer personas, you’ll gain valuable insights into customers’ needs, pain points, and preferences to guide the experience design process. Moreover, you’ll explore creating customer journey maps to identify touchpoints and ensure seamless interactions throughout the entire customer experience. By conducting empathy interviews with customers, you’ll deeply understand their emotions and motivations, fostering a customer-centric design approach. The workshop also covers rapid prototyping to quickly test and iterate design solutions based on real customer feedback. Upon completing this training, you’ll be equipped with effective design-thinking principles, leading to improved customer satisfaction, increased loyalty, and executive support. Your organization will benefit from a customer-centric approach, resulting in an enhanced reputation, higher customer retention, and a competitive edge in the market. By implementing a seamless and emotionally engaging customer experience, you’ll build strong and lasting relationships with your customers while continually adapting to their evolving needs and preferences.
- Part 3 Month 5 Innovation Strategy – Highly innovative companies experience a remarkable 17.7% return on investment (ROI), compared to a mere 2.7% for low innovators (Conference Board study). An effective innovation strategy is the key to generating novel ideas, products, or processes that drive positive change and deliver value to the organization. Without a clear innovation strategy, companies face stagnation, missed opportunities, and heightened vulnerability to competition. Failing to adapt to evolving market demands and stay ahead of competitors can lead to loss of market share and declining revenue. For instance, a technology company lacking a coherent innovation strategy might fall behind rivals, miss emerging trends, and struggle to meet customers’ changing needs. Consequently, they risk losing market position and talent due to a lack of exciting projects. This workshop focuses on essential elements of a successful innovation strategy and how to implement them effectively. Participants will learn the importance of fostering an idea incubator, tapping into employees’ and stakeholders’ creativity and expertise. Deep customer insights and feedback will be highlighted to identify unmet needs and innovation opportunities. Embracing a fail-fast culture, encouraging experimentation, and learning from failures will be emphasized. Forming cross-functional teams will foster diverse perspectives and enhance creativity. Techniques for spotting opportunities, such as tracking market trends and agile prototyping, will be explored. Participants will gain insights into implementing a systematic process for evaluating and prioritizing ideas based on feasibility and potential impact. Completing this training equips participants to create an innovation-friendly environment. Expect enhanced creativity, accelerated development of groundbreaking ideas, increased adaptability to changing market conditions, and improved competitiveness in the industry. Empowered by these insights, participants and their teams will drive innovation more effectively, securing a sustainable competitive advantage.
- Part 3 Month 6 Technology Roadmap – It is a strategic framework that propels businesses into the future by leveraging cutting-edge technology to enhance organizational effectiveness and efficiency. It guides businesses in adopting and integrating advanced technological solutions to achieve their objectives and stay competitive. No technology roadmap leads to falling behind competitors, inefficiencies, limited innovation, and unmet market demands. For instance, a professional service company without such a plan struggled to optimize its processes while competitors embraced automation, artificial intelligence, and data analytics. This resulted in higher operating costs, reduced service quality, and declining customer satisfaction, leading to a loss of market share. In the workshop, participants will learn to develop and implement a successful, customized technology roadmap. They will explore technology integration, effectively blending advanced solutions into existing processes for improved efficiency. Data optimization will enable attendees to harness the power of analytics and AI for data-driven decision-making and better business outcomes. The workshop will emphasize creating a well-connected technology ecosystem that encourages collaboration and cross-functional integration. It also covers technology upskilling, providing essential training to employees for effective technology utilization. A customer-centric approach will be highlighted, using technology to gather insights and enhance the overall customer experience. Participants will gain expertise in developing a detailed technology roadmap aligned with the organization’s strategy and objectives. Upon completion, participants will be equipped with the knowledge and tools to craft a well-crafted technology roadmap, driving their organizations towards greater efficiency, enhanced innovation, improved customer experience, optimized resource utilization, and a forward-looking approach that embraces emerging technologies and opportunities.
- Part 3 Month 7 Resource Allocation – Is a crucial aspect of efficient deployment of financial, human, and technological resources to optimize performance and strategy implementation. Without effective allocation and funding typically leads to project delays, compromised quality of deliverables, decreased competitiveness, and missed growth opportunities. For instance, a technology company aiming to launch a new product line may suffer from inadequate resource allocation, resulting in insufficient funds for research and development, limited manpower for product testing, and outdated technology infrastructure, ultimately impeding the product’s timely market entry and competitive advantage. In this workshop, participants will gain comprehensive knowledge about strategic resource allocation and its pivotal role in successful strategy deployment. The workshop will cover various key components and strategies, such as resource mapping to analyze existing resources and identify gaps, resource forecasting to predict future resource needs based on growth plans, and the establishment of a resource allocation framework that considers strategic priorities, risk assessment, and return on investment. Attendees will also learn about resource flexibility to adapt quickly to changing circumstances, resource collaboration to optimize sharing across departments, and resource performance metrics to measure impact and identify areas for improvement. The training will further emphasize resource scalability to meet changing demands, resource risk assessment for contingency planning, and resource technology integration to streamline allocation processes. Upon completion of this training, participants will possess the necessary tools and insights to effectively allocate resources for strategy deployment, so that individuals will contribute significantly to their team and organization’s growth and success, while maximizing return on effort (ROE) and investment (ROI).
- Part 3 Month 8 Institutional Capabilities – Your secret weapon for outshining rivals. Institutional capabilities encompass the integrated set of people, processes, and technology that empower organizations to surpass competitors and achieve sustainable success. They serve as the bedrock for strategic decision-making, efficiency, and innovation. Failing to cultivate strong institutional capabilities can lead to stagnation, missed opportunities, and an inability to adapt to dynamic market demands, resulting in lost competitive advantage and declining performance. For instance, a technology company lacking capabilities in digital integration and innovation culture may struggle to keep pace with competitors. Inadequate integration of digital tools can cause inefficiencies and delays, hindering responsiveness to market shifts. Similarly, a lack of an innovation culture may hinder breakthrough solutions, leaving the organization trailing behind more agile rivals. This workshop covers essential components for building robust institutional capabilities. Participants will learn about competitive intelligence, talent development, customer insights, collaborative ecosystems, adaptive governance, data-driven decision-making, and incentive alignment. Through this exploration, attendees will gain skills in gathering and analyzing competitor data, fostering a learning organization, improving customer-centric approaches, establishing flexible governance structures, leveraging data analytics, implementing real-time monitoring, and aligning incentives for collaborative success. After completion, participants will have the knowledge and tools to transform their team’s and organization’s capabilities, make informed strategic decisions using competitive intelligence and data-driven insights. They will foster a culture of continuous learning and innovation, enhance customer experiences, streamline processes, adapt to changing market conditions, and promote sustainable practices for long-term viability. These outcomes will benefit individuals, teams, and the organization, leading to superior performance and a competitive edge in their respective markets and operating environments.
- Part 3 Month 9 Change Leadership – It focuses on ensuring the successful adoption and integration of a redesigned model across an organization. Its purpose is to drive and support the transformational efforts required to implement changes effectively and achieve the desired outcomes. Without effective change leadership, organizations encounter resistance from employees, lack of alignment, low engagement, and ultimately, failure to realize the intended benefits of the change. For instance, imagine an insurance company introducing a new digital transformation initiative aimed at streamlining operations and enhancing customer experience. However, without strong change leadership, employees may resist the changes due to fear of the unknown, skepticism about the benefits, or concerns about their job security. This resistance can create roadblocks, hinder progress, and even lead to project failure. In this workshop, you will learn a comprehensive set of skills and strategies to become an effective change leader and guide your organization through successful transformations. The workshop content includes various modules, such as resistance management, where you’ll learn to identify potential sources of resistance and develop proactive strategies to address them. Additionally, you’ll discover how to create a communication strategy that ensures consistent and transparent messaging to keep everyone informed and engaged throughout the change process. Stakeholder engagement will be another crucial topic, teaching you how to involve key stakeholders early on, increasing ownership and buy-in for the changes. The workshop will cover change readiness assessment to help you identify areas that may need additional support and preparation, ensuring a smoother transition. Moreover, you’ll learn how to foster a continuous improvement culture, facilitate knowledge transfer between teams, provide leadership development training, and celebrate milestones to boost morale and motivation. Feedback mechanisms will be discussed, allowing you to gather valuable insights for iterative improvements. Upon completion of this training, you will have the expertise to lead change effectively, overcoming resistance and fostering a supportive culture. You’ll be able to identify and empower change champions, conduct risk assessments, and use data-driven decision-making to monitor progress. Your capacity to align incentives and conduct post-implementation reviews will drive sustained success. In conclusion, this workshop on change leadership is a transformative opportunity for both participants and their organizations. Participants will gain valuable skills to navigate complex changes and lead with confidence, resulting in successful implementation and optimized processes. The organization will benefit from smoother transitions, increased employee engagement, and the realization of the intended benefits from the redesigned model, ultimately driving overall organizational excellence.
- Part 3 Month 10 Governance Integration – Effective governance shields organizations from reputational disasters. It places transparency, accountability, and ethical conduct at the forefront, striving to establish a robust framework aligned with best practices and ethical standards. This fosters stakeholder trust and ensures long-term organizational sustainability. Without such integration, organizations risk facing decreased stakeholder confidence, reputational damage, regulatory non-compliance, heightened unethical behavior, and compromised decision-making processes. For instance, a company’s failure to implement proper governance integration can lead to mistrust among stakeholders due to a lack of transparency in financial reporting and decision-making, resulting in declining investor confidence. Furthermore, the absence of clear ethical guidelines may lead to fraudulent practices, triggering legal repercussions and tarnishing the company’s reputation. In this workshop, participants will learn a comprehensive approach to governance integration across key areas. Emphasis will be placed on governance audits to assess effectiveness and ensure adherence to transparency, accountability, and ethical standards. Stakeholder engagement will be explored, fostering open communication and feedback solicitation for increased transparency. Ongoing ethics training will be stressed to promote ethical conduct, decision-making, and conflict of interest awareness among employees and leaders. Additionally, the integration of social responsibility initiatives and risk management practices into governance will be covered, along with promoting board diversity to enhance decision-making processes. Upon completing this training, participants will have a thorough understanding of governance integration and its essential role in transformation programs. They will possess practical tools and strategies to establish a governance framework prioritizing transparency, accountability, and ethical conduct. Ultimately, this workshop empowers participants to confidently implement governance best practices, safeguard stakeholder trust, ensure regulatory compliance, and foster a positive organizational culture.
- Part 3 Month 11 Risk Mitigation – Is not a luxury but a necessity in today’s volatile operating environment, aimed at minimizing the impact and likelihood of failure. It involves a comprehensive approach that combines various strategies to identify, assess, and address potential risks proactively. By implementing risk mitigation measures, organizations can safeguard their projects and operations, enhance decision-making, and optimize outcomes. Failure to adequately address risk mitigation can lead to major delays, cost overruns, reputational damage, and, in extreme cases, complete failure. For instance, imagine a multinational company launching a new product without a well-defined risk mitigation strategy. They encounter unforeseen supply chain disruptions, leading to delays in production and missing the launch deadline, affecting stakeholders, employees, and overall profitability. In this workshop, you will learn a comprehensive set of risk mitigation techniques to bolster the success of your projects and initiatives. The content covers a range of strategies, including risk diversification, contingency reserves, stakeholder mapping, scenario planning, risk identification, and risk response planning. Upon completion of this training, you will have a thorough understanding of how to identify, assess, and prioritize risks relevant to the OpEx program. You will be equipped to develop well-structured risk response plans, ensuring the team is prepared to handle potential challenges effectively. By implementing these risk mitigation strategies, you will enhance the overall performance of the OpEx program, increase resilience to external factors, and promote a culture of proactive problem-solving within your team or organization. Ultimately, these outcomes will translate into improved success rates, reduced financial losses, enhanced stakeholder trust, and long-term sustainability.
- Part 3 Month 12 Corporate Culture – More than 80% of employees believe a strong corporate culture boosts job satisfaction and performance by promoting desired values, behaviors, and norms for a future-proof work environment. It fosters unity, shared purpose, and engagement, leading to increased productivity and success. Conversely, a weak culture results in directionless teams, reduced morale, increased turnover, and diminished performance. Without a unifying vision, employees may have conflicting priorities and work in silos, hindering collaboration and innovation. The absence of a strong culture leads to a disengaged workforce, resulting in missed deadlines, subpar product quality, and a loss of competitive edge. In this workshop, you will learn practical strategies to strengthen corporate culture to drive OpEx. The culture canvas technique will enable you to create a visual representation of the desired values, behaviors, and norms, facilitating effective communication and reinforcement of the corporate culture. Appointing influential employees as culture ambassadors will ensure that these values are embodied and promoted throughout the organization, serving as role models for others to follow. Employee empowerment drives decision-making and ownership, which stimulates innovation and adaptability. Additionally, you will discover how to integrate the desired values into recruitment, performance evaluations, and recognition programs, aligning behaviors with the corporate culture. Continuous feedback mechanisms will be established to assess the culture’s effectiveness and adjust based on employee input, ensuring the culture remains relevant and impactful. Upon completion of this training, you will have the tools and knowledge to shape a robust corporate culture that fosters operational excellence. By implementing these strategies, you can expect to witness increased employee satisfaction, higher productivity, and a stronger sense of purpose and belonging within your team or organization.
Methodology
Operational Excellence
Program Planning
A successful Operational Excellence (OpEx) program requires thorough planning to ensure its success. The initiator must take charge and assess the program’s purpose to determine whether there is a need for a significant change. The purpose of the program should be clear and actionable, with a burning desire to make a step change, improve an unsatisfactory situation, or achieve a breakthrough.
Once the purpose of the program is defined, the initiator should envision the desired outcome, picturing how the world would be improved after successful implementation. This involves assessing whether the goal is worth pursuing, and if it is, identify the effort and investment required to achieve it. This process should also involve identifying any obstacles that must be overcome and who needs to be convinced and committed to making the program successful.
A critical component of preparing for an improvement program is to develop a detailed kick-off document that outlines the program’s purpose, benefits, and timeline. This document should be shared with key stakeholders, including senior management and front-line employees, to ensure alignment and buy-in from everyone who will be impacted.
Communication is also key to successful change management, such as the execution of an OpEx program. Program leaders should communicate the need for change, the expected outcomes, and the benefits of the program to all stakeholders. It is essential to engage with stakeholders early and often to ensure their input is taken into consideration and to build support for the program.
Additionally, the initiator should identify the critical resources required to execute the OpEx program successfully. This includes identifying potential skills gaps and resource shortages, investing in the necessary training and development programs to ensure that employees have the skills and knowledge required to support the program’s goals.
In conclusion, a successful OpEx program requires a clear understanding of its purpose, buy-in from all stakeholders, effective communication, and adequate resources to execute the program successfully. By following these steps, the initiator can increase the likelihood of success and achieve their desired outcomes by developing a clear and concise kick-off document to ensure all stakeholders are on board, behind the mission, and support the program.
Program Development
The development of an Operational Excellence (OpEx) program involves several steps after stakeholders have been aligned and the program has been committed to. The first step is creating a formal strategy-deployment document that aligns breakthrough objectives with mission, strategies, resources, tactics, projects, metrics, and people. This strategy map, also known as the “X-Matrix,” ensures that all critical elements are thoroughly thought through, well-defined, and connected. By doing so, it ensures that the OpEx program can be explained from various angles, such as what objectives will be achieved, when, by whom, and how.
After completing the strategic planning, the next step is to define the baseline and target to quantify the performance gap and develop a clear and concise problem statement based on a well-aligned key metric. The problem statement could be to increase output from 320 to 400 units per day, reduce average waiting time from 18 to 5 minutes, boost quality from 4 to 5 Sigma, increase customer satisfaction on a five-star scale from 2.8 to over 4.5, or to satisfy a market from 78% to 98%. Once the problem is defined and the performance gap is quantified, the causes and drivers will be analyzed. Logic-trees are used to identify the causal relationships between actions and conditions on physical, human, and system domains. These driver-trees are then used to develop countermeasures that will reduce or eliminate the performance gap, creating a tangible gain on the program metric.
After confirming the effectiveness of the countermeasures, the next step is to develop the future-state design and simulate the resulting performance gain. Once the simulation is complete, the OpEx program is ready for pilot testing. This approach ensures that the OpEx program is well-planned, measurable, and effective, with a clear understanding of its objectives, metrics, and targets. By following this process, teams can achieve breakthrough results in operating performance, customer satisfaction, quality, and market share that they have never thought possible before.
Program Implementation
Successfully implementing an Operational Excellence (OpEx) program requires specific key factors to be present. Without them, the program is likely to fail or fall short. These factors include a clear vision, alignment among stakeholders, sufficient resources, a detailed master plan, the right skills, incentives to act, and clear communication.
Having a clear vision is essential to avoid confusion about the direction and reasons for change. The vision should be shared widely, attainable, realistic but challenging, measurable, adaptable, and strong enough to withstand daily pressures to maintain the status quo.
Alignment is crucial in gaining buy-in, especially for flat organizations and self-directed teams. True alignment is achieved when people fully invest themselves in pursuing the agreed-upon direction as their own. This is important especially for the management and supervisor-level between senior management and frontline.
Sufficient resources, including time, people, budget, information, tools, and equipment, prevent frustration. Budgeting resources early in the process and managing the scope strictly avoids “scope creep” and “goal creep” that would demand additional resources and potentially derail the project or program.
A clear roadmap in the form of an action plan makes progress measurable, prevents false starts, and frequent course corrections. It specifies desired results and deliverables, lays out a timeline with specific milestones and tasks, and defines how goals are to be reached, along with who is responsible for them.
Providing training to build required skills eliminates anxiety, a common reaction to change. Starting training early in the process ensures that required skills are in place when needed. These include not only technical skills to perform a certain task or process, but also inter-personal and managerial skills to execute the desired change.
Offering incentives that are directly linked to the vision in a measurable way and benefit those affected by the change in a tangible way prevent apathy and slowness. Tangible and intangible incentives, such as monetary benefits, personal achievement, prestige, or choice motivates people to act.
Clear communication prevents disconnects and creates engagement. It ensures that everyone is aware of the goal, its importance, the scope and location, the people involved and impacted, the timeline and milestones, the plan to achieve the goal and the metrics to track progress, and the business case that defines costs and benefits. Keeping everyone informed allows people to get involved and have a stake in the success.
In conclusion, successful implementation of an OpEx program requires careful planning and execution. By addressing these factors, the target organization can effectively manage change and achieve its breakthrough objectives, while avoiding common pitfalls such as resistance, frustration, anxiety, apathy, and disconnects. Ultimately, a well-executed OpEx program will drive significant gains in agility, efficiency, productivity, quality, and customer satisfaction, helping organizations stay competitive and sustain success.
Program Review
An Operational Excellence (OpEx) program is a systematic approach to improving operational efficiency and effectiveness within the target organization. To evaluate the effectiveness of an OpEx program, it is important to review its status and impact on the organization.
The first step in reviewing the status of an OpEx program is to gather data on its implementation. This includes reviewing the number of sprints and deliverables that have been successfully completed, the overall program relative to its timeline, and the resources that were required to complete them. It is also important to consider the feedback from stakeholders, such as customers and employees who have actively participated in the program, as well as feedback from managers, owners, and external stakeholders.
Once the data has been collected, it will be analyzed to identify areas of success, shortfalls, and where improvements are needed. This structured review will help to determine whether the OpEx program is achieving its goals and delivering value to the organization. For example, if the program has resulted in a reduction in time or effort to deliver the same or better outcome, it may be considered successful.
Another important aspect of reviewing the status of an OpEx program is to evaluate its impact on the organization. This includes looking at changes in customer satisfaction, employee engagement, and financial performance. For example, if the program has led to increased customer satisfaction and improved financial performance, it may be considered a success. Reviewing the financial impact is always key to ensure that resources are being used effectively and that the expected return on investment (ROI) is being achieved.
It is also important to consider the long-term impact of an OpEx program. This includes evaluating whether the improvements made during the program have been sustained over time and whether the program has led to a culture of continuous improvement within the organization.
In conclusion, reviewing the status and impact of an Operational Excellence program is essential to evaluating its effectiveness and ensuring that it is achieving its goals. By gathering and analyzing data on program implementation and evaluating its impact on the organization, managers can identify areas of success and areas where improvements are needed to ensure that the program continues to deliver value in the long term, not only economically, but also in terms of environment, social and governance (ESG).
The Blueprint for Achieving Excellence
The pursuit of excellence is an ongoing journey, especially in a dynamic world where customer expectations and market demands constantly evolve. To stay relevant and achieve long-term profitability, organizations must continuously raise the bar and set higher standards. Operational excellence (OpEx) is the driving force behind this journey, encompassing a comprehensive framework for continuous improvement. In this article, we will delve into the methodology behind OpEx implementation and explore the components to build an effective improvement machine.
Five Steps to Systematic Improvement
Over the past two centuries of industrialization, operational performance has experienced remarkable growth in quality, speed, and productivity, fueled by human ambition and innovation. The drive for improvement is unending, as challenges such as defects, disruptions, and delays persist. These challenges, however, present us with opportunities to create a better world that brings greater value to humanity. We will now explore the five components of the OpEx improvement process and understand how it operates.
Step 1: Initiation
The OpEx journey begins with identifying the “What?”, an unsatisfactory situation, an unresolved problem, or an untapped opportunity. The leadership team, comprising executives such as CEO, CFO, COO, initiates improvement initiatives based on customer needs and business demands. These top-down requirements are supplemented by internal ideas and benchmarks from external sources. They shape the improvement agenda and are an important input for the planning phase, defining the “What?” needs to be improved.
Step 2: Planning
A cross-functional improvement team evaluates inputs based on their potential impact and strategic fit and determines the “How?” to improve. Prioritization is done by considering factors such as effort required and the expected benefits. The most promising proposals are subjected to formal analysis, where benefit potential, required resources, and implementation timelines are estimated. This analysis culminates in the creation of a project charter, which is a concise document summarizing the project’s business case and milestones for execution. The charter is presented to the leadership for approval, funding, and support to initiate the improvement cycle.
Step 3: Improvement
The heart of the process is the “Improvement Engine”, which operates continuously and completes one revolution every month. Each improvement cycle (sprint) is thoroughly planned to ensure successful execution within the allocated resources, risks and constraints. The time is fixed, but the content can be adjusted as needed. With each revolution, another sprint is performed until the entire project charter is fully implemented and the defined requirements are met.
Step 4: Validation
The progress of each initiative is measured on an ongoing basis to determine if there is “Impact?”, using leading and lagging indicators. Leading indicators, such as task completion or schedule adherence, are monitored in real-time, enabling the team to identify potential barriers early and resolve them quickly. Lagging indicators are utilized to assess task effectiveness based on their impact on quality, speed, and effort. Since improvements often take time to materialize fully, tracking both leading and lagging indicators is essential. It is akin to monitoring the actual speed, remaining battery level, and distance driven in a vehicle.
Step 5: Closure
At the completion of each improvement cycle (monthly sprint), the gap between required and actual performance is measured to determine if “Gains?” have been achieved. Operational indicators directly measure the performance improvements in terms of defect rate, rework level, return rate, process time, lead time, or service level. To communicate the results effectively to the leadership team, these operational measures must be translated into the financial domain. This translation defines cost savings resulting from reduced material and energy consumption and paid hours. It also takes into account cost avoidance resulting from diminished risks, non-performance costs, and deferred investments, as well as incremental profits derived from greater productivity.
This comprehensive OpEx process drives excellence through continuous improvement. By systematically tackling challenges and optimizing resources, you can achieve remarkable improvements that benefit both their operational efficiency and overall performance, ultimately leading to enhanced value for all stakeholders involved – a better product or service for customers, a more stable operation for the company, a higher return on investment for the owners, a stronger partnership with suppliers and a better workplace for employees.
The Engine that Drives the Improvement Machine
Achieving excellence requires a continuous process. While Deming’s PDCA cycle (Plan, Do, Check, Act) works well for basic problem-solving, it falls short in handling more complex initiatives. To drive excellence effectively, a proven method begins with project initiation and planning, goes through continuous learning and execution, and concludes with impact validation and closure. This process is powered by the four-cylinder improvement engine, completing one revolution per month. Within this cycle, the team engages in structured learning and execution, ensuring measurable progress through preparation, development, implementation, and review.
Cylinder 1: Preparation
In the first step, participants dedicate themselves to thorough preparation. They study and familiarize themselves with the challenge at hand, delving into theoretical concepts and guiding principles relevant to the topic. This initial stage equips them with the necessary knowledge and understanding, setting the stage for the upcoming learning and application activities.
Cylinder 2: Development
Moving on to the second step, the focus shifts to development. Participants come together in interactive workshops to share information, align their views, build essential skills, and collaboratively develop solutions. Through hands-on exercises and real-world examples, they gain confidence and knowledge, empowering them to effectively drive the improvement initiatives.
Cylinder 3: Implementation
The third step centers around implementation. Armed with the newly acquired skills and capabilities, participants apply their learning to real-world environments. They take charge of improvement initiatives and put theory into practice, actively ensuring that the knowledge translates into tangible results and added value.
Cylinder 4: Review
Finally, the last step is dedicated to review. Participants assess the outcomes of their implementation efforts and gather feedback. This critical analysis enables continuous improvement and adjustment, allowing participants to adapt their approaches and drive sustained value over time.
By following this well-structured 4-step execution cycle, the improvement engine keeps people focused and projects on track. It fosters a culture of continuous learning and empowers individuals to become proactive drivers of positive change in their areas of responsibility.
The Daily Scrum to Overcome Barriers and Procrastination
In the world of continuous improvement, challenges and unexpected events are always present. Even the best plans can be disrupted by unforeseen circumstances. This is where the notorious duo of Murphy and Parkinson come into play, posing risks to project success. Murphy’s Law warns us that anything that can go wrong will go wrong, while Parkinson’s Law reminds us that work expands to fill the time available. However, there’s a powerful tool at our disposal to tackle these risks head-on – the daily Scrum meeting – explained in the following video:
By adopting daily Scrum meetings, also known as daily stand-ups, project teams can maintain focus, adapt quickly, and tackle issues in real-time. These short, time-boxed gatherings are a cornerstone of Agile project management, particularly in the Scrum framework. Let’s explore how these daily meetings serve as an effective solution to mitigate the uncertainties brought forth by Murphy’s Law and the inefficiencies associated with Parkinson’s Law. Through communication, adaptability, transparency, timeboxing, commitment, and progress tracking, daily Scrum meetings keep the project engine running smoothly, fostering a path to successful project outcomes.
Murphy’s Law
Murphy’s Law states that “anything that can go wrong will go wrong.” In the context of project management, this law reminds us that unforeseen issues and challenges are inevitable. No matter how well a project is planned, there will always be uncertainties and unexpected events that can impact the project’s progress and success. These could include delays, resource constraints, scope changes, technical difficulties, and more.
Parkinson’s Law
Parkinson’s Law is the adage that “work expands to fill the time available for its completion.” In the context of project management, this law suggests that tasks and activities may take longer to complete if there are no defined time constraints or deadlines. Without proper time management and clear deadlines, projects may suffer from inefficiencies, lack of focus, and procrastination, leading to delays and missed targets.
How Daily Scrum Meetings Rectify Risks
Daily Scrum meetings, also known as daily stand-ups, are a key component of the Agile project management framework, especially in Scrum. These short, time-boxed meetings are held daily with the project team to discuss progress, impediments, and the plan for the day. They serve as a powerful tool to address the risks associated with Murphy’s Law and Parkinson’s Law:
1. Addressing Murphy’s Law:
• Regular Communication: Daily Scrum meetings promote open communication among team members, allowing them to identify potential issues and risks early on. If any problems arise, they can be addressed promptly, reducing the chances of major setbacks.
• Agile Adaptability: Agile methodologies, including Scrum, embrace change as a natural part of the development process. By inspecting and adapting daily, the team can quickly respond to unforeseen challenges and adjust their approach accordingly.
• Transparency: During the Daily Scrum, team members share their progress and any roadblocks they are facing. This transparency enables the team to collaborate and offer support to resolve issues collectively.
2. Addressing Parkinson’s Law:
• Timeboxing: Daily Scrum meetings are typically kept short, usually lasting 15 minutes or less. This time constraint encourages teams to focus on essential updates and prioritize the most critical tasks for the day.
• Commitment and Accountability: Each team member shares their commitments for the day during the Daily Scrum. By doing so, they publicly commit to completing specific tasks, which increases their sense of accountability and helps prevent procrastination.
• Progress Tracking: Daily Scrum meetings provide a daily checkpoint to review progress against the project’s goals and deliverables. This helps in identifying any deviations from the plan and ensures that the team stays on track.
In summary, Daily Scrum meetings are a valuable practice in managing improvement projects, as they foster communication, transparency, and adaptability within the team. By addressing issues proactively and maintaining a sense of urgency and accountability, these meetings help mitigate the risks associated with Murphy’s Law and Parkinson’s Law, ultimately leading to more successful project outcomes. Daily Scrums are especially important to keep the critical design and implementation phases on track.
Application Example: Improving Customer Satisfaction
The following case illustrates how a manufacturing company tackles declining customer satisfaction and increased defects through the OpEx improvement process. We will explore the five key steps – initiation, planning, improvement, validation, and closure – and see how they lead to manufacturing excellence and enhanced profitability.
1. Initiation
Imagine a manufacturing company that has been facing declining customer satisfaction due to increased product defects. The leadership team identifies this dissatisfactory situation and initiates an improvement initiative. They analyze customer feedback, conduct internal brainstorming sessions, and also benchmark against industry competitors to understand the scope of improvement needed.
2. Planning
The cross-functional improvement team evaluates the inputs and identifies a proposal that aims to reduce defects through process optimization. They estimate the potential impact, required resources, and implementation timeline. The team then creates a project charter, outlining the business case and milestones. For instance, they plan to implement statistical process control (SPC) techniques and invest in employee training.
3. Improvement
In this example, the improvement engine involves conducting monthly sprints to implement the proposed changes. In the first sprint, the company focuses on training employees in SPC methods. Subsequent sprints involve integrating SPC into the production process. Each sprint builds on the previous one until the full charter is executed, and the defect rate decreases significantly.
4. Validation
Throughout the improvement process, the company uses leading indicators, such as real-time monitoring of defect reduction tasks. For instance, they track the percentage of employees trained in SPC and the number of defects detected and corrected daily. They also use lagging indicators, like the overall defect rate, to assess the effectiveness of their efforts over time.
5. Closure
After several improvement cycles, the company successfully reduces defects, leading to a significant improvement in product quality. They translate these operational improvements into financial gains by calculating the cost savings resulting from reduced rework and material consumption. Additionally, they consider the cost avoidance from avoiding product recalls and the potential incremental profits due to increased customer satisfaction and repeat business.
Through the OpEx improvement process, the manufacturing company successfully reduces defects, improves product quality, and achieves higher customer satisfaction. By following this framework, you can drive excellence and create greater value for all stakeholders.
Build Your Improvement Machine!
Operational excellence is more than just a buzzword; it’s a systematic and disciplined approach to continuous improvement. We’ve explored the methodology behind OpEx implementation, showing how it drives excellence. From project initiation to validation, the OpEx process empowers organizations to tackle challenges, optimize resources, and achieve remarkable improvements. Embracing a culture of continuous improvement enhances operational efficiency, delivers better products and services, and creates greater value for all stakeholders. Pursuing excellence allows organizations to thrive in a rapidly changing world and make a positive global impact. Let follow the detailed process outlined in this OpEx program to build a highly-effective improvement machine that propels us into the future.
Industries
This service is primarily available to the following industry sectors:
Manufacturing
Operational Excellence (OpEx) has been an essential strategy in manufacturing for several decades. It involves optimizing production processes to achieve high levels of efficiency, quality, and safety. OpEx is applied in a wide range of manufacturing industries, such as assembling vehicles, airplanes, cameras, phones, and producing food, furniture, garment, machines.
One of the main benefits of OpEx is improved productivity. By identifying and eliminating waste in production processes, companies can achieve higher output levels with the same resources or the same output with fewer resources. This, in turn, leads to increased profitability and a competitive advantage in the market.
OpEx also improves quality control by reducing errors and defects in production. This not only saves money by avoiding the costs associated with rework and scrap but also improves customer satisfaction by delivering higher quality products. This is a major focus of many OpEx programs.
Moreover, OpEx helps manufacturers to achieve compliance with regulatory requirements, such as environmental regulations or workplace safety regulations. By implementing best practices and standard operating procedures (SOP), companies can ensure that they are meeting regulatory requirements and avoiding potential penalties.
The outlook for OpEx in manufacturing is promising. As manufacturing becomes increasingly automated and digitized, companies can use data analytics and artificial intelligence to optimize their production processes continually. This allows for even more precise identification and elimination of waste, further improving efficiency and quality control.
In addition, OpEx is being applied more and more beyond the production line to optimize supply chain processes, such as procurement and logistics, to reduce costs, inventories, and inflexibility, shortening delivery times. It is also being used to optimize administrative processes, such as human resources or accounting, to improve productivity and reduce overhead costs.
In conclusion, Operational Excellence is a powerful tool for improving productivity, quality control, and compliance in manufacturing. Its future development potential is vast, as companies increasingly rely on digital technology and automation. By applying OpEx principles to a broader range of processes, manufacturers can achieve even greater efficiency, quality, and profitability.
Technology
Operational Excellence (OpEx) is a widely used strategy in the leading technology industry. Its roots can be traced back to the manufacturing industry, but it has since evolved to be applicable in various sectors. The focus of OpEx in technology is on optimizing processes, systems, and tools to achieve high levels of efficiency, quality, and innovation.
Currently, OpEx is applied across the technology industry, including software development, hardware development, production, and service delivery. In software development, both OpEx and Agile principles are used to optimize the entire software development lifecycle, including planning, design, testing, deployment, and maintenance. In hardware development and production, OpEx is used to optimize prototyping, pilot testing, production processes, including supply chain management, quality control, and assembly. In service delivery, OpEx is used to optimize customer support, incident management, and service delivery processes.
The specific benefits of OpEx in the technology industry are numerous. Firstly, it helps companies to reduce costs by identifying and eliminating waste and variability in their processes. This, in turn, leads to higher profitability and a competitive advantage in the market. Secondly, OpEx helps to improve product quality and reliability, reducing the risk of product recalls or customer dissatisfaction. Thirdly, OpEx helps to improve customer experience by optimizing service delivery processes, ensuring that customers receive timely and high-quality support.
The outlook for OpEx in the technology industry is bright. As technology continues to evolve rapidly, companies must continually innovate and improve their processes to stay ahead of the competition. This includes embracing digital transformation, such as automation, artificial intelligence, and data analytics. OpEx can be used to optimize these new technologies, ensuring that companies can achieve the full potential of their investments.
Moreover, OpEx can be applied beyond traditional technology processes. For example, it can be used to optimize development and administrative processes, such as finance, human resources, and procurement. This, in turn, leads to improved efficiency and productivity across the entire technology organization.
In conclusion, Operational Excellence is an essential approach in the technology industry. Its history, current application, and outlook demonstrate that it is a powerful tool for optimizing processes, systems, and tools. The benefits it creates, including cost reduction, quality improvement, and customer satisfaction, are essential for companies to stay competitive in a rapidly evolving market. The future development potential for OpEx in the technology industry is significant, as companies continue to embrace digital transformation and seek new ways to optimize their processes.
Biotechnology
Operational Excellence (OpEx) plays a critical role in helping the biotech and pharma industry evolve to meet the increasing demands of patients and investors. While OpEx concepts have been well-established for decades, they have mainly been applied in manufacturing. However, there is significant potential for OpEx to expand its scope and scale from downstream to upstream processes.
OpEx helps the biotech and pharma industry achieve consistency in quality not only in manufacturing but also in development and trials. This is particularly important for regulated products, as any variability in quality can have serious consequences for patient safety. OpEx helps companies to identify and eliminate any potential sources of variability in their discovery, trials, production, and quality control, ensuring that products are of consistently high quality.
OpEx also helps the biotech and pharma industry reduce costs while maintaining quality. Developing new drugs is a time-consuming and expensive process. Any cost savings that can be achieved without compromising quality can make a significant difference to a company’s bottom line. OpEx helps companies to identify and eliminate waste in development and management, reducing costs while maintaining quality.
Improving efficiency is critical to the biotech and pharma industry’s success. Time-to-market is crucial, and any delays can have serious consequences for both patients and the company’s financial performance. Operational Excellence helps companies to identify and eliminate inefficiencies in their processes, reducing the time it takes to bring products to market.
Regulatory compliance is a significant challenge for the biotech and pharma industry. Failure to comply with regulations can have serious consequences for patient safety and the company’s reputation. OpEx helps companies to implement systems and processes that ensure compliance with regulatory requirements.
Finally, OpEx encourages continuous improvement. The biotech and pharma industry is constantly evolving, and new technologies and approaches are constantly emerging. OpEx helps companies to identify areas for improvement and implement changes that keep them at the forefront of the industry.
In conclusion, OpEx is essential for the biotech and pharma industry to achieve its goals. By focusing on continuous improvement in quality, cost, efficiency, compliance, and innovation, companies can stay competitive and deliver life-changing treatments to patients worldwide. Its importance will only increase in the future to meet increasing demands for stringent compliance, extreme quality, and end-to-end traceability.
Automotive
Operational Excellence (OpEx) is a management philosophy and business strategy to drive operational performance while creating a culture of continuous improvement that enhances quality, efficiency, and profitability. The automotive industry has a long history of embracing operational excellence principles. In the early 1900s, Henry Ford implemented the assembly line, which revolutionized the manufacturing process and allowed for the mass production of automobiles. Since then, operational excellence has been a driving force in the industry, leading to advances in production techniques, quality control, and supply chain management.
Today, operational excellence is applied across all aspects of the automotive industry, from design and development to manufacturing and distribution. This approach has resulted in significant benefits for the industry, including increased productivity, improved quality, reduced waste, and enhanced customer satisfaction.
One specific area where operational excellence has had a significant impact in the automotive industry is in Lean Manufacturing. This methodology is focused on eliminating waste, reducing cycle times, and improving productivity by empowering workers to identify and eliminate problems in production and assembly processes. By applying Lean Manufacturing principles, automotive companies have been able to streamline their operations, reduce costs and cycle times, and massively increase efficiency.
Another area where operational excellence has created benefits for the automotive industry is in supply chain management. With global supply chains becoming increasingly complex, operational excellence has helped companies to manage their suppliers more effectively, reducing lead times, and improving inventory management. This has resulted in more efficient production processes, reduced costs, and improved customer satisfaction.
The outlook for operational excellence in the automotive industry is strongly positive, with new technologies and approaches continuing to emerge. For example, the industry is currently adopting the Industry 4.0 technologies, such as Artificial Intelligence (AI), Digital Twin for components and vehicle as a system, and the Internet of Things (IOT), to further enhance operational efficiency and productivity.
Overall, operational excellence has been and will continue to be a critical factor in the success of the automotive industry. By focusing on creating a culture of continuous improvement, automotive companies can enhance their competitiveness, improve their bottom line, and deliver high-quality products that meet the evolving needs of their customers.
Locations
This service is primarily available within the following locations:
Zurich, Switzerland
Zurich (Zürich) is a global center for business, technology, and manufacturing, with a long history of excellence in these fields. Companies operating in Zurich benefit from the city’s highly skilled workforce, advanced infrastructure, and business-friendly environment. Due to comparatively high labor cost, companies from the area have a strong commitment to operational excellence (OpEx) to improve their operational efficiency and profitability.
With strength in business, Zurich is home to a wide range of industries, from banking and finance to pharmaceuticals and engineering. The city is a hub for international business, with many of the world’s leading companies having a presence in the city. Zurich’s business-friendly environment and low corporate taxes make it an attractive location for companies looking to establish a foothold in Europe.
Zurich is also a global center for technology and innovation, with many of the world’s leading tech companies establishing a presence in the city. Google, Microsoft, IBM, and other major tech firms have research and development centers in Zurich, taking advantage of the city’s talented workforce and research institutions. The city has also become a hub for startups in the technology sector, with many innovative new companies emerging in areas such as blockchain, artificial intelligence, and robotics.
Despite being a high-cost area, Zurich is also a center for manufacturing, with a focus on precision engineering and high-tech manufacturing. The city has a long history of excellence in this field, with many of the world’s leading engineering and manufacturing companies having a presence in the city. Zurich’s highly skilled workforce and advanced infrastructure make it an ideal location for companies looking to establish manufacturing operations in Europe.
An operational excellence (OpEx) program helps companies operating in high-cost locations, such as Zurich, to improve their operational efficiency and profitability. These programs are designed to identify areas of inefficiency and waste within a company’s operations and to develop strategies for improvement. By implementing an OpEx program, companies can improve their productivity, reduce costs, and increase profitability.
An OpEx program also helps companies in high-cost countries, such as Switzerland, to improve their quality and customer satisfaction. By identifying areas of improvement and implementing strategies to address these issues, these companies can improve their products and services, leading to higher levels of customer satisfaction and loyalty, which is key to remain competitive in Switzerland.
San Jose, United States
San Jose, located in the heart of Silicon Valley, is a center for manufacturing striving for operational excellence (OpEx). The city and its surrounding areas are home to a range of high-tech manufacturing companies, producing everything from semiconductors to medical devices. San Jose’s commitment to OpEx makes it an ideal location for companies looking to improve their manufacturing efficiency and profitability.
The area’s strength in manufacturing is dating back to the early days of the tech industry. Today, the city is home to a range of high-tech manufacturing companies, including semiconductor manufacturers, medical device manufacturers, and aerospace companies. These companies benefit from the city’s highly skilled workforce, advanced infrastructure, and business-friendly environment.
Because of its strategic location in the heart of Silicon Valley, the city provides easy access to a range of suppliers, customers, and partners. The OpEx program helps factories and technology centers in Bay Area to improve their operating speed and efficiency by identifying areas of inefficiency and waste and to develop strategies for systematic improvement. By implementing an OpEx program, those operations improve their productivity, reduce costs, and increase profitability – key to remain competitive in the Bay Area.
San Jose’s strength in manufacturing and technology makes it an ideal location for companies looking to establish an operation in California. Factories and technology centers in San Jose benefit from the city’s highly skilled workforce, advanced infrastructure, and business-friendly environment, making it an ideal location for growth and expansion. And the OpEx program helps these companies to take advantage of these benefits, while improving time-to-market (TTM), yields, overall operating efficiency (OOE), and customer satisfaction, creating a competitive advantage from OpEx in California.
Singapore, Singapore
Singapore is a small island nation located in Southeast Asia. Despite its small size, it has become a global leader in manufacturing and technology, making it an ideal location for factories, laboratories, technology centers, and engineering firms to set up an operation there. With the help of an operational excellence (OpEx) program, these companies can not only improve speed and efficiency, but also gain a tremendous competitive advantage.
One of Singapore’s key strengths is its well-established manufacturing sector. The country is known for its precision engineering and high-tech manufacturing capabilities, particularly in the areas of electronics, semiconductors, and biomedical devices. The government has made significant investments in infrastructure, education, and technology to support this sector, and it has paid off. Today, Singapore is home to over 7,000 manufacturing companies, many of which are global leaders in their respective fields.
In addition to manufacturing, Singapore has also emerged as a hub for technology and innovation. The country has invested heavily in research and development, and it has a thriving startup ecosystem. Many multinational technology companies, such as Google, Facebook, and Amazon, have established regional headquarters in Singapore, attracted by the country’s skilled workforce and business-friendly environment. Singapore is also home to several technology parks and incubators, where startups and entrepreneurs can access funding, mentorship, and resources to help grow their businesses.
Given these strengths, it is no surprise that many factories, laboratories, technology centers, and engineering companies are choosing to establish a presence in Singapore. However, to truly thrive in this competitive environment, these companies must embrace OpEx to improve the agility, quality, and efficiency. It involves identifying and eliminating defects, delays, disconnects, and duplications by improving processes, while creating a culture of continuous improvement.
By implementing an OpEx program, companies can improve their quality, reduce costs, and increase productivity. This is particularly important in Singapore, where labor and real estate costs are high. By optimizing their operations, companies can maximize their return on investment and stay competitive in the global marketplace. Fortunately, Singapore offers many resources for companies looking to implement an OpEx program. The government has established several initiatives to support businesses in this area, such as the Lean Enterprise Development Scheme (LEDS) and the Enterprise Development Grant (EDG). These programs provide funding and training to help companies implement OpEx practices and improve their operations.
In conclusion, Singapore’s strength in manufacturing and technology, combined with its business-friendly environment, make it an attractive location for factories, laboratories, technology centers. By embracing OpEx strategies, those firms will reduce costs, losses, and lead times, creating a competitive advantage from operating in Southeast Asia.
London, United Kingdom
The financial industry is one of the main drivers of the UK economy, and London is the heart of this industry. With a long history of excellence in finance, London is home to many of the world’s leading banks and financial institutions. These companies rely heavily on operational efficiency to remain competitive and profitable. The implementation of an OpEx program helps these companies to optimize their processes, reduce losses, and streamline their operations. This, in turn, leads to increased profitability, improved customer satisfaction, and a more efficient workforce.
The service industry is another significant sector in the UK, accounting for a significant portion of the country’s GDP. London is a hub for many service industries, including healthcare, education, hospitality, and professional services. These industries also benefit from implementing OpEx programs to improve their operational efficiency. For example, healthcare providers use OpEx programs to streamline patient care processes, reduce wait times, and improve patient satisfaction. Similarly, hospitality providers optimize their guest services, improve their amenities, and reduce costs to increase profitability.
The implementation of an OpEx program also benefits companies in the UK by improving their supply chain operations. London’s advanced logistics and transportation infrastructure make it an ideal location for companies looking to establish supply chain operations in Europe, despite of Brexit. By implementing an OpEx program, companies can optimize their supply chain processes, reduce lead times, and improve inventory management. This leads to more efficient and cost-effective supply chain operations, which in turn can increase profitability and improve customer satisfaction.
In addition to the financial and service industries, other sectors in the UK also benefit from implementing OpEx programs. For example, manufacturing companies in the Kingdom are increasing use OpEx programs to improve their production processes, reduce losses, and increase efficiency. An leading example is the infrastructure sector, which applies OpEx principles to modern methods of construction (MMC), delivering buildings, bridges, railways at half the cost and lead-time, compared to traditional way of working. The benefits of an OpEx program are not limited to a particular industry or sector, but rather can be applied to any business operation looking to improve its efficiency and profitability.
In conclusion, companies operating in the UK can benefit from implementing OpEx programs in various industries, including finance, service, manufacturing, and retail. By identifying opportunities to improve processes and implementing strategies to capitalize on them, companies can increase their efficiency, reduce costs, and improve customer satisfaction – all of which are essential to become and remaining competitive in the Kingdom.
Munich, Germany
Germany is a country with a rich history and a vibrant culture, known for its technological advancements and engineering expertise. Among its many strengths, Germany is particularly renowned for its manufacturing industry, which has been the driving force behind the country’s economic success for decades. With a focus on precision and quality, German manufacturers have established a reputation for producing high-quality products that are in demand around the world.
One area of Germany that is particularly strong in manufacturing and technology is Munich and the surrounding region. Home to several world-class engineering companies, research laboratories, and technology centers, this area is at the forefront of innovation and plays a key role in driving the German economy.
To maintain its competitive edge in the face of global competition, companies operating in the region are increasingly turning to operational excellence (OpEx) programs to improve competitiveness through world-class operations. By adopting best practices in process improvement, quality control, and lean manufacturing, these companies streamline factories and technology centers by reduce waste, strain, variability – the three major losses.
The benefits of an OpEx program are manifold. By improving operational efficiency, companies can increase their productivity, reduce costs, and improve their competitiveness in the global marketplace. This is particularly important for manufacturing companies, which must constantly adapt to changing market conditions and evolving customer needs, while operating in a high-cost country, such as Germany.
In addition to the economic benefits of an OpEx program, there are also important environmental and social benefits. By reducing waste and improving resource efficiency, German companies can lower their carbon footprint and contribute to a more sustainable future, while lowering costs from lowering energy consumption. Moreover, by investing in the skills and capabilities of their employees, these companies create more rewarding and fulfilling workplaces that contribute to the well-being of their communities.
One example of a company that has successfully implemented an OpEx program in the Munich area is Siemens, one of Germany’s leading engineering companies. With a focus on OpEx and a commitment to quality, Siemens has been able to maintain its position as a global leader in engineering and technology. By adopting best practices in process improvement, quality control, and lean manufacturing, Siemens has been able to improve its operational efficiency and increase its competitiveness in the global marketplace.
Another example of a company that has benefited from an OpEx program is BMW, the world-renowned manufacturer of luxury automobiles. With a focus on quality, innovation, and sustainability, BMW has established itself as a leader in the automotive industry. By implementing best practices in process improvement, quality control, and lean manufacturing, BMW has been able to improve its operational efficiency, reduce waste, and improve its environmental performance.
In conclusion, Germany’s strength in manufacturing and technology is a key driver of the country’s economic success, and the Munich area is at the forefront of this industry. By adopting an OpEx program, companies in this region can improve their business operations, increase their productivity, and contribute to a more sustainable future. With a commitment to continuous improvement and a focus on quality, German companies are well-positioned to maintain their competitive edge in the global marketplace.
Copenhagen, Denmark
Copenhagen, the capital city of Denmark, is known for its progressive and innovative approach to urban design and sustainability. In addition to its reputation as a livable city, Copenhagen is also a hub of manufacturing and technology in the Scandinavian region. With a focus on simplicity and quality, Danish manufacturers have established a reputation for producing high-quality products that are in demand around the world.
The factories, laboratories, technology centers, and engineering companies in the Scandinavian area are well positioned to benefit from an operational excellence (OpEx) program. By adopting best practices in process improvement, quality control, and lean manufacturing, these companies streamline their operations, reducing waste, strain, and variability, while improving their bottom line.
The benefits of an OpEx program are manifold. By improving operational efficiency, Scandinavian companies ^increase their productivity, reduce costs, and improve their competitiveness in the global marketplace. This is particularly important for manufacturing companies, which must constantly adapt to changing market conditions and evolving customer needs.
In addition to the economic benefits of an OpEx program, there are also important environmental and social benefits. By reducing waste and improving resource efficiency, companies lower their carbon footprint and contribute to a more sustainable future. Moreover, by investing in the skills and capabilities of their employees, companies can create more rewarding and fulfilling workplaces that contribute to the well-being of their communities.
One example of a company that has successfully implemented an OpEx program in the Scandinavian area is Novo Nordisk, a leading healthcare company that specializes in diabetes care. With a focus on innovation and sustainability, Novo Nordisk has been able to maintain its position as a global leader in healthcare. By adopting best practices in process improvement, quality control, and lean manufacturing, Novo Nordisk has been able to improve its operational efficiency and increase its competitiveness in the global marketplace.
Another example of a company that has benefited from an OpEx program is Vestas, a leading manufacturer of wind turbines. With a focus on renewable energy and sustainability, Vestas has established itself as a leader in the wind energy industry. By implementing best practices in process improvement, quality control, and lean manufacturing, Vestas has been able to improve its operational efficiency, reduce waste, and improve its environmental performance.
In conclusion, Copenhagen is a hub of manufacturing and technology in the Scandinavian region, and the factories, laboratories, technology centers, and engineering companies in this area are well positioned to benefit from an OpEx program. By adopting best practices in process improvement, quality control, and lean manufacturing, these companies can improve their business operations, increase their productivity, and contribute to a more sustainable future. With a commitment to continuous improvement and a focus on quality, Danish companies are well-positioned to maintain their competitive edge in the global marketplace.
Program Benefits
Production
- Process standards
- Streamlined flow
- Labor efficiency
- Equipment reliability
- Quality improvement
- Waste reduction
- Variability reduction
- Inventory reduction
- Schedule adherence
- Safety compliance
Management
- Strategic alignment
- Reliable processes
- Repeatable results
- Agility boost
- Efficiency gain
- Risk reduction
- Enhanced morale
- Learning organization
- Customer satisfaction
- Competitive advantage
Finance
- Complexity reduction
- Resource efficiency
- Capacity utilization
- Productivity boost
- Profitability gain
- Cost savings
- Cost control
- Risk mitigation
- Cash optimization
- Compliance adherence
Testimonials
Givaudan
Mauricio Graber, President: “I worked with Mr. Muenzing over the last 3+ years in his consulting function as Global Head of Givaudan Flavours Lean initiative. During this period he created and led the global OpEx/Lean Program, “Journey to world-class efficiency”. As part of our profitability improvement initiative he focused on sustainable reduce costs and cycle times. The program delivered significant bottom line impact from embedding lean principles across 20 prioritized manufacturing sites; it further evolved as an engine for cultural change and performance improvement.”
Mercedes Benz
Martin Daum, CEO Truck Division: “You have accomplished something big that keeps on delivering. Production runs at an excellent level and new improvements are noticeable every single day. Your work has definitely beard fruits. Thanks again for your engagement and commitment.”
Navico
Jens-Thomas Pietralla, CEO: “Mr. Muenzing has been instrumental in the process of fundamentally improving Navico, the global market leader in marine electronics for the recreational boating segment. He is committed and results-driven, having spent 12 months helping Navico transform its manufacturing operations globally to ensure successful operations (with focus on operational excellence OpEx). Specifically, his input and efforts were fundamental in effecting key improvements at three of our manufacturing sites in Mexcio, Europe, and Asia Pacific. A s a management consultant, he showed relentless commitment to improving Navico’s manufacturing and supply chain operations, reflecting his personal focus on “navigating to results”. Mr. Muenzing has built on Navico’s strengths to optimize the manufacturing-model overall, implementing step-changes and giving recommendations to leverage existing capabilities and culture. His optimism and “can-do” attitude combined with a creative out-of-the-box approach for initiating change has been a great catalyst in driving Lean-implementation of three plants in Mexico, New Zealand, and Norway, ensuring over $5 million bottom-line in savings and throughput-increase. The participant feedback in these change programs has been exceptionally positive. In Mr. Muenzing’s role as Interim manager for our manufacturing plant in Mexico, which employs 1500, and has a $1 million per day throughput, he led the team in a crisis-like situation to meet stretch-targets, increasing output from $14 Million to $22 Million within two months. The results speak for themselves: The combined impact of these efforts to EBITDA was approximately $8 Million. I can confidently recommend Mr. Muenzing for any position or assignment in manufacturing excellence and supply chain management. I firmly believe his skills and experience will measure up to any challenge.”
Trioworld
Carsten Valentin, Divisional President: “Mr. Muenzing has been instrumental in developing the Trioworld Continuous Improvement Model and he continues to add value to our operational excellence effort. He possesses the ability to support us in taking our high-level strategy and make it operational, thus driving real change and sustainable performance improvement.”
Autoliv
Stephane Nancy, Operations Director EMEA: “Mr. Muenzing has been hired by my company to analyze our weaknesses and help our team to improve quality performance in manual and aspect product for automotive. In a complex supply chain with systemic issues from product and process development, he helped us to refuel our quality foundation by leading, teaching quality standards. With the application of Operational Excellence and Six Sigma, we recovered a good level of quality shipped and quality made in high and challenging business. The method of his analysis and problem solving are flexible and adaptable to complex ecosystem and financial challenges. I would like to thank him for his complete support and leadership in international environment. Great job and positive long-term mindset developed as an outcome of the program.”
Simrad
Henning Risholm, SVP Manufacturing: “Overall I was very satisfied with what we accomplished during this short period. I would say that Mr. Muenzing’s version of Operational Excellence is more extreme than we have learned before from our consultants and I think I know why. You must be extreme to get real changes and I believe 100% in your way. Many of our employees know now very well the principles and how to apply them, the management team is skilled to further develop the site. We met all my expectations and more…! The operation is improving day by day: last week over 1800 units, up from 400 units average before, see below chart. Thanks a lot for what you have done with my people and organization, it would never have been possible without your skill and experience. You pushed us over a hill that we couldn’t have done ourselves, neither with our existing consultants. I think my management team has now more to teach to our consultants then vice versa.”
Givaudan
Rudy Niquille, COO: “Mr. Muenzing had been hired as a consultant to act as the Global Head of our OpEx/Lean program. As part of his mandate he contributed to the following achievements: developing and leading the implementation of a global Lean program, as part of a wider initiative, to ensure sustainable reduction of costs and cycle times, as such aiming at delivering significant bottom line impact through embedding Lean principles across 20 manufacturing sites; developing a team of experts, training Lean champions in dedicated boot camps, leading to the certification of 450 Yellow-, Green-, and Black Belts; identifying performance improvement potentials and guiding local teams in the execution as well as building capability, so that the bulk of the sites attained a Silver certification; creating and deploying best practices for problem solving and performance management. Finally, our OpEx/Lean program further evolved as an engine for cultural change and performance improvement. In a nutshell Mr. Muenzing’s skills and capabilities enabled the creation of value beyond the initial expectations. Further, he is an experienced change agent. His work made a significant contribution to our organization, and I can only recommend him for any operations improvement program, especially those with a global footprint.”
Trioworld
Matthias Alexander Schwarz, Head of Sales: “I took part in a workshop where Mr. Muenzing led a dedicated, cross-functional team into understanding, describing, revising current and finally defining future customer service standard operating procedures. Within several sessions, he guided the workshop into an effective and target-oriented workflow. His knowledge and international experience gave inspiring and significant input. Mr. Muenzing kept all members of the group involved, motivated, and focused during the sessions by a clear structure on how to approach and analyze actual and future workflows. He supported an open and constructive discussion to understand and value individual views and experiences. His guidance towards our goal to define the way on how to increase both service and efficiency was outstanding, always in a friendly and productive atmosphere. I highly appreciate his support and communication skills, always aiming improvement and reducing complexity for the benefit of the customer and internal stakeholders. We also agreed on how to measure the efficiency of the current status on our way into customer service excellence. It was a great experience, and I am looking forward already today to the next opportunity to work with Mr. Muenzing on service excellence.”
Wrist Ship Supply
Management Team Houston: “Very professional and quick to understand the needs. If you need a ‘kick in the butt’ then this program will start your sense of urgency, open your eyes, and set your priorities straight. Highly competent and established, and with real practice examples, not only theoretical.”
Norsk Gjenvinning
Hans Fredrik Wittusen, Director of Strategy: “Highly knowledgeable and experienced Lean change agent with a strong ability to introduce and facilitate substantial and lasting improvements at our processing plants. In an operational setting with no previous Lean experience he has quickly earned the trust and commitment of plant managers and operators alike, and his stepwise approach and strong coaching skills have resulted in strong internal motivation and popular demand for starting Lean transformation programs at additional sites. We are very satisfied with the approach and results.”
Navico
Gerald Walle, CFO: “I hired Mr. Muenzing to help me solve a manufacturing crisis in a plant producing less than 50% of planned output despite overtime and excess spending. The problems were caused by problems with a new product line launch and widespread issues in the manufacturing strategy. He played an absolutely major role in tripling the volume of the new product line and almost doubling the overall volume of the plant within a month, and then in bringing lean manufacturing approaches to the operation over the next few months. A year later the plant is performing very well with dramatically increased productivity and quality and at the same time a significant reduction in costs. Mr. Muenzing worked in this plant for about 7 months and then went on to other plants in the group and the management team of the plant (somewhat changed) built very successfully on the platform he had started.”
Veolia
Kolbjørn Akervol, District Manager: “Working with Leanmap has built a stable structure for continuous improvement in our company. Their unique ability to understand, cooperate with and develop people at all levels and departments throughout the organization assures that we achieve results beyond expectations, and leaves behind teams of highly dedicated and motivated employees that will continue to grow and develop our company Lean style. To summarize, I would use just one word: word-class!”
Takeda
Jad Sakr, Head of Quality Services: “I really enjoyed the training and found it very insightful; it is a wise combination of theory and hands-on practice.”
Franke
Global Workshop: “The session was awesome; I am still in shock. It was a very big surprise in the sense of how effective and simple it looks, which makes me feel very capable to apply these things right away at my workplace. Real passion behind the whole initiative, very good involvement of people, knowledge is really passed on to participants. Peer feedback on projects was very helpful. Good to reverse rolls and provide feedback for others. Case studies are very effective in getting the point across.”
Landis & Gyr
Executive Team: “I very much appreciate what Mr. Muenzing has done. We never had such focus on quality before. Congratulations for a good presentation in the executive meeting – it was a really great wake up call. Thanks to the program, more than 400,000 units were already updated. Customers are excited about the smooth deployment; they are very happy. The biggest risk therefore has been mitigated. The result in EMEA has been excellent and we want Mr. Muenzing’s help to implement the same in APAC.”
More detailed achievements, references and testimonials are confidentially available to clients upon request.
Client Telephone Conference (CTC)
If you have any questions or if you would like to arrange a Client Telephone Conference (CTC) to discuss this particular Unique Consulting Service Proposition (UCSP) in more detail, please CLICK HERE.