Manufacturing Productivity
The Appleton Greene Corporate Training Program (CTP) for Manufacturing Productivity is provided by Mr. Greene Certified Learning Provider (CLP). Program Specifications: Monthly cost USD$2,500.00; Monthly Workshops 6 hours; Monthly Support 4 hours; Program Duration 12 months; Program orders subject to ongoing availability.
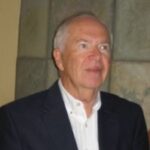
Personal Profile
Mr. Greene is a Certified Learning Provider (CLP) at Appleton Greene and has managerial experience in manufacturing, industrial engineering, and R&D.
He has achieved a Bachelor of Science in Industrial Engineering and been a registered Professional Engineer in three states.
He has industry experience within the following sectors: Manufacturing, Pharmaceuticals, Consumer Goods; Fast Moving Consumer Goods, and Food & Beverage.
He has had commercial experience within the following countries: United States of America, more specifically including Dallas, Salt Lake City, Las Angeles, Irvine, and San Diego California: and in Buenos Aires Argentina and Rio de Janeiro Brazil.
His professional achievements include: Headed division or corporate industrial engineering for three Fortune 250 companies; ITT Latin America, Abbott Labs, and Ray-Ban when it was a division of Bausch & Lomb. Has authored nine books and written dozens of articles relating to productivity.
His service skills incorporate: productivity of direct and indirect labor, production management, cost reduction, process improvement, facility planning and layout.
To request further information about Mr. Greene through Appleton Greene, please Click Here.
(CLP) Programs
Appleton Greene corporate training programs are all process-driven. They are used as vehicles to implement tangible business processes within clients’ organizations, together with training, support and facilitation during the use of these processes. Corporate training programs are therefore implemented over a sustainable period of time, that is to say, between 1 year (incorporating 12 monthly workshops), and 4 years (incorporating 48 monthly workshops). Your program information guide will specify how long each program takes to complete. Each monthly workshop takes 6 hours to implement and can be undertaken either on the client’s premises, an Appleton Greene serviced office, or online via the internet. This enables clients to implement each part of their business process, before moving onto the next stage of the program and enables employees to plan their study time around their current work commitments. The result is far greater program benefit, over a more sustainable period of time and a significantly improved return on investment.
Appleton Greene uses standard and bespoke corporate training programs as vessels to transfer business process improvement knowledge into the heart of our clients’ organizations. Each individual program focuses upon the implementation of a specific business process, which enables clients to easily quantify their return on investment. There are hundreds of established Appleton Greene corporate training products now available to clients within customer services, e-business, finance, globalization, human resources, information technology, legal, management, marketing and production. It does not matter whether a client’s employees are located within one office, or an unlimited number of international offices, we can still bring them together to learn and implement specific business processes collectively. Our approach to global localization enables us to provide clients with a truly international service with that all important personal touch. Appleton Greene corporate training programs can be provided virtually or locally and they are all unique in that they individually focus upon a specific business function. All (CLP) programs are implemented over a sustainable period of time, usually between 1-4 years, incorporating 12-48 monthly workshops and professional support is consistently provided during this time by qualified learning providers and where appropriate, by Accredited Consultants.
Executive summary
Manufacturing Productivity
History
Frederick Taylor in the late 1900s was the first proponent of Scientific Management. In the following few decades, he had some visible and very effective assistance from a notable few but not too many other people; in developing the concepts of scientific management. Henry Ford was conspicuously cost conscious, in product design and manufacturing innovation.
Heroes to Industrial Engineers are Frank and Lillian Gilbreath, primarily for their work in time study and work measurement. As we review the writings of Frank Gilbreth literally over 100 years ago, he suggested that a primary tool to improve productivity is to reduce waste. One of the two tenants of the Toyota Production System is, you guessed it, to reduce waste.
Taylor and Frank Gilbreth both started with a stopwatch. After all, arguably the most important question in manufacturing is “how long does the job take?”
Our tool to determine priority also goes back more than 100 years, to Vilfredo Pareto who first quantified that a small number of Italian citizens possessed a large amount of Italian wealth. The concept has been broadened to show that, within a given set of elements, a small number of individual elements constitutes a very large portion of total value. We use the Pareto Principle to find productive opportunities.
Otherwise, until World War II there was little organized recognition of, or progress in, manufacturing productivity. Then because of the amounts of armaments required and a national sense of urgency, productivity which led to output was a focus of manufacturing, often skipping the theory phase and going directly into practice. Some of these oldies but goodies are still around because their value has been proven.
Productivity is measured as output divided by input. Therefore, any action taken to increase output, or decrease input, results in higher productivity.
“Productivity” can relate to any element of corporate activity; direct and indirect labor, overhead, materials, equipment, facilities, services. Direct labor cost is quite often not a large percentage of product cost, but direct labor can a good starting point for productivity improvement, for two reasons: 1) Labor has a cost of its own even if not large, and 2) the major function of labor is to operate equipment and processes efficiently and to optimize their capability; to build the product. So, good idea, let’s produce, providing output on time to meet the market demand. Let’s improve labor and equipment productivity, over a wide range of constituent parts.
The latter half of the 20th century and partway into the 21st have evidenced change on such a prolific scale that that it can hardly be defined. Semiconductors, computers, electronics in general, the space age, the growth of Asia as a supplier of products of all kinds. For manufacturers, evolving computers and electronics and programs have introduced the mechanisms to control production more accurately. A negative is that the rate of technology change that is possible has tended to obscure the crystal ball that tells us what comes next.
With the changes, the worldwide manufacturing arena is not the same as it has been, which suggests that participants in the arena may feel it necessary to make further changes on their own part.
Current Position
There are very many facets to productivity, and very many circumstances in manufacturing which test the capability of management to optimize productivity. Aha, that means that there will also be very many opportunities for improvement.
And usually in the dynamic world of manufacturing, the most important issues and opportunities have to do with the financial picture. But the manufacturing problem of the day may also be related to labor supply, or to uncertainties in the supply chain, or to the ability to have employees report to work in an environment free of infectious disease. Welcome to the future.
The classic productivity mechanisms for manufacturing have not gone out of style, if anything computer capabilities and electronics have simplified and augmented their use. New concepts are proposed routinely, with broad or narrow application. We have available constructive, productive solutions to a wide range of challenges, in a multitude of industrial settings.
Frank Gilbreth over 100 years ago suggested that a primary tool to improve productivity is to reduce waste. One advantage of our current situation is that several very effective methods with which to reduce waste have been developed. The Pareto Principle zeroes in on the most productive opportunities, to get the biggest bang for the buck.
Any productivity improvement relies on an assumption that is often not spoken. The assumption is that any given project is expected to be beneficial assuming all other factors are equal. And of course other things are never equal; any improvement will be expected to perform within the circumstances of the time however much different from the assumptions. Really useful solutions then will have a short fuse, they will be selected and designed to contribute quickly. A better longer-term solution may be proposed as well but the emphasis will be on rapid results.
Today the situation in international trading is a significant concern. There are mechanical concerns, due to the COVID epidemic; on one hand worldwide demand has been affected and on the other hand individuals are prevented from working; there may be a shortage of oceangoing vessels, or a backup at seaports, individuals may choose to work remotely. There are broader implications too, international tensions and the supply chain imbalances both of which may be short term or longer term.
There is great interest in productivity; of personal productivity, of output in general, and in productivity which targets business and industry. But interest does not necessarily translate into specific practical action.
Work measurement, whether a formal system or otherwise, can be a primary factor in control of labor cost and activity. If measurement is formal, (and continually maintained) then management has an objective knowledge of the activity. But it is not uncommon that production tasks have not actually been observed and measured, that rates in use are from past performance or estimate, or are no longer reflective of actual equipment, methods, materials, specs. In such a case, costs may be incorrectly stated such as production worker pay; manufacturing controls such as scheduling of product or forecasting or number of people required may be off; some Key Performance Indicators that management uses will be incorrect because the value of direct labor content is not up to date.
Future Outlook
Are you looking for a program laden with technology or buzz words? This isn’t it. This program, Manufacturing Productivity, zeros in on the heart of manufacturing, namely what happens on the manufacturing floor, the warehouse dock, the machine shop site. To describe production in one word, try Dynamic. The one production constant is change.
In the productivity arena, one size does not fit all. That is why this program offers many differentiated processes; they tend to be straightforward; specialized with a concentrated focus, yet they reinforce one another.
Initially, we will assess as-is conditions to determine just what needs attention, although probably you have an idea already. Prioritize issues, judge resources available, set a plan.
It is likely that individuals with different responsibilities at different organizational levels will attend specific portions of the multi-functional workshops, in relationship to the responsibilities of their specific job functions.
Two prime productivity tools of all those available, are the Pareto Principle and a pillar of Frank Gilbreth and the Toyota Production System, eliminate waste. Pareto tells us that a few factors will contribute the majority of cost; of problems; of opportunity. First then let’s identify, quantify and understand those principal elements in your circumstance. Then we’ll start to eliminate waste in subsequent steps of this program.
Typically, a cost reduction effort targets direct labor. That’s often not the right target by the way, because there are usually larger costs. But labor has a cost even if small, and perhaps more importantly labor operates machinery and processes. We want labor to be productive and effective in order to manufacture your product.
The key tool to achieve productivity, alone and in conjunction with other tools, is work measurement.
Production labor rates may be current, or set years ago or only estimated in the first place. But regardless of their accuracy, they are routinely entered into systems such as standard cost, variance analysis, production scheduling, capacity planning, hiring and training. (Your Key Performance Indicators depend on accurate production rates.) To allow sound management decisions, set production rates on today’s methods from which waste has been removed, (workshop #3) with today’s equipment, specs, technology and product mix.
Workshop # 2 will address work measurement; how to create reliable engineered standards, develop applications and gain benefits. A subsequent workshop identifies placement and use of work measurement data within existing systems.
An early workshop will address production constraints, processes to quantify, relieve, and manage them. The constraints workshop, along with the waste removal one, will provide rapid attention to central manufacturing concerns.
One workshop will focus on Outcomes; not just output but also timing, quality, product mix. We will discuss reporting, keeping the score, and which modifications and extensions are possible.
A common interruption to production has to do with batch sizes and product changeovers. A workshop will be dedicated to minimizing the number of batch changes in the first place and expediting the changeover process.
One workshop will address the specific subject of formal cost reduction throughout an organization, offering a wide range of possibilities. A workshop will offer processes of plant layout, flow, and space utilization because arrangement of people, materials and equipment is at the very heart of business productivity, in an organization of any size; engaged in just about any endeavor.
Work measurement can be effective in indirect labor operations of maintenance, materials handling, and quality control. One workshop will address these procedures and processes.
A workshop will summarize the multitude of productivity techniques and theory available, both modern and the golden oldies. As you choose to fit your objectives and cost structure, consider also your organization’s culture and capability.
The final workshop will address the accomplishments of the preceding sessions. Come join us.
Curriculum
Manufacturing Productivity – Part 1- Year 1
- Month 1 Situation Assessment
- Month 2 Establish Work Measurement
- Month 3 The Pareto Principle and Remove Waste
- Month 4 Productivity Constraints
- Month 5 Outcomes
- Month 6 Improve the Workstation
- Month 7 Reporting, and Work Measurement Rates in Production Systems
- Month 8 Batch Size and Changeover
- Month 9 Cost Reduction
- Month 10 Management Planning and Control Processes
- Month 11 Plant Layout, Flow, Space Utilization
- Month 12 Results Review
Program Objectives
The following list represents the Key Program Objectives (KPO) for the Appleton Greene Manufacturing Productivity corporate training program.
Manufacturing Productivity – Part 1- Year 1
Month 1: Situation Assessment
Workshop 1: Baseline assessment of the as-is situation.
The client will have received in advance a list of as-is assessment questions, and may well suggest others. The questions address a wide variety of manufacturing circumstances, because productivity is affected positively or negatively by many different factors. There are two primary objectives; one to collect information about today’s status, but also to learn what are considered to be the more important issues. Maybe even some that are not on the list. For instance, within any group of people familiar with operations there might be common consensus about particularly troublesome operations. Be sure that the subject is identified and discussed.
Or, which equipment is the most expensive, the one you would least like to replace? Refer also to reports and KPI’s to highlight issues.
Consider not only direct operations but also support, laboratory, testing, inspection, material handling, changeover, maintenance which delays product delivery. Very early on and continually remove any potential stigma from this analytical exercise. This exercise is merely to identify the fact, not to cast any blame at all.
During the body of today’s workshop, a knowledgeable representative of the client will provide responses to the questions raised. These responses to the as-is assessment, and the ramifications of the answers, can then be the focus of discussion.
This workshop will offer perspectives of the primary management concepts from which the program and the various processes are founded.
As the manufacturing productivity process is constructed around work measurement, the client is requested to suggest which internal department, existing or to be established, will perform work measurement activities.
Month 2: Establish work measurement
The purpose of this workshop is to establish and institutionalize the fundamental concept of this entire program, namely work measurement. We will briefly define work measurement and list its benefits, but the main purpose will be to explain exactly what to do and how to so it, and to establish work measurement, including the qualified people to do it and the processes which they will use.
A rate quantifies the time for an average trained operator, working at good speed and effort, to perform a sequence of operations. Work measurement is a statistical process, and it requires training to be able to establish rates correctly. The processes for training practitioners will be defined.
The first step in the standard setting process is to remove all waste from the operations observed, and processes to remove waste will be the subject of workshop number 2.
The next rate-setting step is to observe the operation and determine the time which required to perform. Next, we will “read” the studies and convert the raw times into averages, for all of the work elements involved, add in non-cyclical elements and allowances for break, lunch and so forth to create a standard rate.
Rates must be filed and published, and the values given out to departments who used them in their reports and calculations. Rate maintenance, to assure that they are continually up to date, will be continually necessary. The rates will be applied, and actual output compared to expectations periodically, perhaps daily or weekly.
Month 3: The Pareto Principle, and Remove Waste
Two primary subjects will be presented which are fundamental to good productivity. In each case they will be discussed, and specific processes illustrated for immediate and future use by the client.
The first subject is to reduce waste. The classic industrial engineering adage has always been to ”remove, don’t improve”. Since one Toyota Production Systems tenet is “remove waste”, this action has become much more visible and popular.
Another subject that is at the heart of improvement is the Pareto Principle. Vilfredo Pareto, a 19th century Neo-Classical economist, mathematically described the unequal distribution of wealth that he observed in the world around him. His observations, known as Pareto’s Principle, has been profitably extended into other fields of inquiry. In business Pareto’s Principle tells us that a few of the inventory items will constitute most of the value; a few processes will give most of the trouble; a few line items will generate most of the cost; a few constraints will control the entire pace of operations. Common terms used to define the principle are “ABC inventory”, or the “80-20 rule”.
Now, in this month we will practice Pareto, and waste removal, by reviewing the problematic existing processes and mechanisms which were found during the as-is evaluation. What were they, how important are they, can we contribute to a solution of the problems they raised by eliminating waste in the correct place?
After waste removal, what short term actions appear which may be used to correct the problems? The leader of this discussion will contribute suggestions as to which of the productivity tools will be particularly effective.
The immediate attention to problem areas in manufacturing will have two purposes. Attention will focus on significant problems, and several different processes will be demonstrated which can be used to plan, operate, control and evaluate manufacturing operations.
Month 4: Productivity Constraints
The lead topic this session will be Productivity Constraints.
Productivity constraints are an aggravating concern. As soon as you identify the primary constraint, and solve it, there will be another primary constraint. Seemingly without end. Constraints can be of different character as well. Immediately you think of a machine as being a constraint, but it could also be of a different nature entirely. It could be for instance a material supply, where a vendor is unable to deliver, and an alternate vendor is not available.
A constraint might be a process for instance, a chemical or biological test that takes an extended period of time. A constraint might be change overs, for product or container size necessary to meet the production schedule for a given product mix.
Although a machine might be generally considered to be a constraint, the real problem may not be the machine but the fact that the manufacturers guidelines for preventive maintenance were not being followed so that the machine was operating less frequently than it was designed to.
A machine might obviously not be a constraint because it has a machine speed and index speed pretty high. and there are four of them. But when one man is assigned to operate the four machines, and because they are of simple design, they jam up a lot, at any given time the output is well less then the index speed.
Unfortunately, there is not a single test, nor form to fill out, that will identify what constraints are. It takes knowledgeable people, investigation and analysis to determine probable culprits.
This workshop will focus on any constraints for which an assessment was made, and any others suggested by attendees. We will define processes to identify, prioritize, and correct constraints.
Month 5: Outcomes
The lead topic this session will be outcomes, not output.
Output is usually good, when producing widgets, gizmos. Production operators will produce what the schedule calls for, with what equipment is set up, using what materials are on hand.
However, for company results, outcome could well be a more desirable. result. So, in Manufacturing Productivity, 11 days we will talk output, this day we talk outcomes.
Output is product being shipped. Outcomes considers, as we manufacture our product, is it –
the right product; a result of new-product development and introduction process,
in the right quantity; a result of inventory, production planning, Just in Time or Just in Case, batch size, processes,
of the right quality, a result of a quality control process with an appropriate level for the product in the marketplace,
at the right time in the right location; a result of plant loading,
with the right features and priced right; a result of product design,
made with appropriate modern equipment and technology, or a result of planning and engineering or a result of inherited processes?
As we discuss these topics, the purpose will be to understand how the client manages certain specific processes which influence manufacturing. The discussion will likely lead to more comprehensive solutions in workshops yet to come.
Month 6: Improve the workstation
The lead topic this session will improve the workstation, where the rubber meets the road.
The earliest recorded interest in scientific management, by Frederick Taylor, was in the late 1800s. The most recent interest in scientific management is going on today. Very early and still today, the workplace itself has been the focus of much attention.
We will explain and evaluate popular and less well-known processes to improve the workplace. The earlier workshop on Constraints will have addressed productivity issues unique to mechanical workstations, so this will focus on less automated production.
Not all improvement processes or created equal. Certainly not all improvement processes are applicable to any given problem. This workshop will identify many tools to insert into the client’s tool belt. so that it will be possible to pull out and utilize the correct one for a particular circumstance.
Month 7: Reporting, and work measurement rates in production systems
This workshop will have two primary topics.
A lead topic this session will be reporting, making information useful to the people who receive it, from floor supervision through staff functions and management.
A useful report will contain reliable numbers but not just in a vacuum; a number should be accompanied by expected results for example. That’s true for other values on a report; reject rate, employee efficiency or productivity, schedule attainment.
For production employees a very valuable value is the production number that they actually produced. The best way to reference that number is as a percentage. And for attainment the magic, expected number is 100%. Different functions and management levels need different results reported, which should lead to tailored reports.
The production floor supervisor must not be overlooked in this process. A supervisor needs to know information that tells how the employees are performing, what the production was, and of any quality problems. Not only actual but also in comparison to what was expected.
A second topic is, utilize work measurement data in operational control.
Traditionally the most value of work measurement is to the operating department whether it be manufacturing, construction, warehousing or another sector. Such techniques and processes will be discussed, and processes demonstrated.
The production department will also find it useful to apply rates to plan capacity, initiate acquisition of needed equipment; calculate actual labor efficiency, (Performance while working), productivity (performance over the entire shift); and equipment utilization.
Operations will be able to quantify output expectations for direct labor; identify and manage constraints; determine crew sizes, balance lines; resolve contested workloads.
Both the maintenance department and the warehouse employ a number of people who are engaged in activities which are repetitive. Repetitive work of any type is receptive to productivity improvement.
Financial departments will find information generated for manufacturing very useful to quantify the labor element of standard cost systems, to administer pay for output plans, conduct usage variance analysis, set overhead allocation (labor portion of quality, maintenance, material handling departments).
Materials management can use the expected hours per task to establish reasonable timing for scheduling production output, estimate cycle times, to calculate changeover cost versus inventory cost carrying costs.
Management strategy, for existing and potential strategy, can be more accurate and objective: Build in the USA? Make / Buy / Vertical integration; justify technology or equipment or automation, calculate equipment utilization. Product pruning, to identify products with low profit margin.
Month 8: Batch size and changeover
The lead topic this session will be batch size and changeover.
Three departments are usually involved in batch size and changeover, and a fourth keeps score and waves the go flag when it is justified. Now, all four departments (production, materials management, maintenance, and quality) are involved in changeovers in two ways; one their people are involved in actual tasks, and secondly some policies and procedures of each department have a bearing on frequency and duration of the changeover itself. The results of the changeover however show up in the reports of only one department namely production.
A materials management department may establish the batch size itself, perhaps from market demand. A constraint in the process such as kettle size, or line speed, or number of people available, or a sterilizer load may set batch size.
Manufacturing does not like changeovers because they interrupt the flow of the product. Operators will just have gotten used to that particular product and its characteristics and the line will be cruising along. Then they’ll have to change. The line may perform its own changeover for instance a label change. Maintenance may be involved in the change if there are size issues, or if the physical characteristics of the line have to be changed.
A product change may involve several time-consuming steps. There are actions possible to mitigate machine changeovers for instance spare machine parts, clean and ready for use.
Paperwork relating to a batch or lot is also involved in changeover, possibly in a major way in a pharmaceutical, or food or beverage, operation.
This workshop session will involve discussions of all of these factors. Batch size determination, frequency, timing and actions will be discussed, and processes demonstrated to quantify and reduce costs. Techniques to expedite change will be defined.
Month 9: Cost Reduction – A Vital Practice in any Economy
Vital, but not always easy. This workshop offers specific ideas on cost reduction; what, where how; for manufacturing, warehousing, industry.
Platitudes and buzzwords alone won’t do the job. Successful cost reduction requires a hands-on approach, to select and prioritize targets, find and effect solutions (literally a line-by-line analysis), consider options, define and implement solutions, measure and brag about results. Your business is unique, but these insights are often useful:
Find and manage constraints, bottlenecks, delays; that extend the cycle time of any activity.
Quantify expectations, measure performance, ask for accountability.
Cherry pick on the floor; look for delay, workload imbalance, high scrap.
Target issues which are relatively easy to find and correct.
Cherry pick at the management level, non-value-added activity, inventory policy that causes changeover or out-of-stock. Match throughput to customer demand, match facilities and workforce to customer demand. Do your internal operating practices or paperwork interfere? Is the quality expectation appropriate, because rocket ships need tighter controls than thumbtacks? Some of these opportunities are not difficult to implement, once they get the attention they deserve.
There is a practice called product pruning. A company decides annually which if any products should be eliminated, based on cost versus income. That is not as simple as it sounds because it requires an accurate knowledge of real costs and net sales prices. Many times, there are individual products crying out for pruning but still in the sales catalogue.
This session will be primarily about ideas for cost reduction. The processes are necessary, but they are pretty simple. What was the unit cost before? What will be the unit cost afterwards? Multiplied the reduction by the volume and that’s the answer.
Month 10: Management planning and control processes
The lead topic this session will be modern management planning and control processes, and the golden oldies, and the inherent conflicts between some processes.
It has it has been a long time since Frederick Taylor started Scientific Management in the late 19th century. He was one of very few who was considering productivity in any sense at that time. In the 21st century there seems to be no end of the people, and qualified people, with proven processes, who contribute to productivity in all endeavors. Including of course Appleton Greene and this program.
In this session we will consider literally dozens of modern, and time-tested, processes; some with wide ranging goals and some with narrowly targeted objectives. Some are proprietary, some are so well known that we quote their tenets offhand.
The Toyota Production System, or TPS, is one of the most well-known tools recently but even it is some 70 years old at this point. It is perhaps best known for JIT, Just in Time inventory system. But, as expressed by Executive Vice President Taiichi Ohno, “The most important objective of the Toyota System has been to increase production efficiency by consistently and thoroughly eliminating waste. This concept and the equally important respect for humanity … are the foundations of the Toyota production system.” Great ideas, Frank Gilbreth thought so when he wrote about them in 1916.
This entire program follows the practice to select perceptive elements or tools, rather than entire systems. A selected portion is more apt to contain pertinent elements for your situation than an entire system.
Month 11: Plant layout, flow, space utilization
Arrangement of people, of materials and equipment, is at the very heart of business productivity; in an organization of any size; engaged in just about any endeavor.
This activity usually goes by the name of layout or facility planning but it includes aspects which are not the same for all operations in the facility. For instance, within production, a primary objective may be to create a short, well-defined flow of materials. In warehousing, flow is important too, but a primary consideration may be “cube utilization”, or the effectiveness which with the volume of the building contains the contents.
Major layouts are often infrequent events, but minor layouts can occur much more frequently. Both frequencies involve a number of processes that simplify, standardize, and optimize the resulting layouts. This workshop will address those processes for immediate and future use. Layout and facility planning can: relieve a jam-packed facility; allow more output with today’s product mix; add output and capacity, facilitate introduction of new products or technology; rearrange to cut through a wasteful “spaghetti” flow; provide area to re-shore production.
Variables in a layout can include the activity involved, the geometry of the facility, equipment, and products; even constraints management, batch sizes and inventory policy. A good layout will provide some open space to facilitate short-term change, and general paths for future expansion.
A key is to maintain output during rearrangement, so a resolution should create both short and long-term activities. Target problems by applying layout technique, then perform moves in a checkerboard sequence, one step at a time.
Month 12: Results Review
The topic this session will be review, of subjects and action assignments throughout the twelve-month series.
The client is requested to have an individuals speak, please, for a functional area, in regard to activities during the twelve months program period. The presentations can include successes, failures, value, intangible benefits and costs, the next step, or other related aspect.
A representative of the organization which has the primary responsibility for performing work measurement activities. That person is requested to speak on the current status of that function, and how it has progressed over the period, and short-term plans.
A financial representative is requested to speak about the status of updated labor rates and standards, and the extent to which they have been built into reporting and financial calculations, and Key Performance Indicators. Are there significant financial findings or revelations from the period? Is there consideration of a pay-for-work plan?
A manufacturing representative is requested to speak about updated labor rates as they are being applied in manufacturing, and the effect which they have had on output, planning, and control.
Other functions may be invited to speak as the client chooses.
The leader will comment on two areas. One will regard impressions of the status of work measurement, its application within the client organization, successes and disappointments. The second comment will be to suggest programs or processes which would be useful to the client, having spent 12 months with the client staff and issues.
Methodology
Manufacturing Productivity
Program Planning
There are many facets to manufacturing productivity, and many circumstances which test the capability of management to optimize productivity.
Just as there are many facets to manufacturing productivity, there are likewise many very successful processes which have been developed historically and recently, with a proven capability to deal with the myriad of complexities. This program will present a selection of these processes.
Productivity is designed as output divided by input, so any act which increases output or reduces input will increase productivity. And any department whether direct or indirect can contribute.
An assessment of as-is circumstances will profile the status of existing factors which affect production costs and potentials, and direct attention to specific needs, issues and processes in the client facility. “Productivity” can relate to any element of activity, labor, materials, equipment, facilities, services.
The program will then use the assessment to suggest specific issues to address, processes to utilize. Removal of waste from activity is a basic step, so an early workshop will initiate that process, as well as the practice to consider the most important concerns first.
We will move through a series off subjects, tools and processes which have a proven history of success. Emphasis will be placed on the results of the assessment, to prioritize actions and processes which are especially relevant.
Usually, the most important factors in production are perceived to be labor or equipment. Labor is often a good starting point, for two reasons: 1) Labor has a cost of its own, and 2) even if labor cost is not a large percentage, the major function of labor is to operate equipment and processes efficiently and to optimize their capability. The program will concentrate on improving labor and equipment productivity.
Program Development
Production areas, or a maintenance shop or a warehouse, are dynamic environments. A common characteristic is sense of urgency, which means that if a specified mechanism is not available for some reason, then another way will be chosen so that work goes on. These one-time occurrences may, in total, change factors of the work environment.
This program centers on the manufacturing floor, or shop, or the shipping warehouse; and addresses elements which contribute to productivity.
Work measurement, whether a formal system or otherwise, is a primary tool to measure labor cost and equipment activity. Work measurement processes are well established. After all, arguably the most important question in manufacturing is, “how long does the job take?”
This program has been developed with work measurement at the center. Work measurement will, in itself, reduce manufacturing cost compared to non-measured rates, past performance, rates which use earlier equipment and methods, or estimates.
Multiple planning and reporting systems depend on labor content, in finance, materials, hiring, forecasting, capacity. Key Performance Indicators often contain a labor content. Obviously, accuracy in the labor standard procedures is vital.
Techniques which are used in work measurement, especially the watch and direct observation of an operation are also the preferred methods to evaluate other productivity processes. Workshop two will present work measurement history and practices to the attendees, as well as detail which will serve as a foundation of training for practitioners. The workshop presentation contains guidance for later administrative aspects of work measurement.
Formal work measurement includes removing waste activity, engineering methods, for current equipment and products and specs.
Formal work measurement, as the client prefers,
a) Can become an incentive, more pay for more output.
b) Can be “Reasonable Expectations”, a formal system to quantify and communicate expectations for people and processes. There is no tie of pay to output. Published reports will itemize actual results by operator.
c) Can be “measured day work”. There is no tie of pay to output. No reporting is performed, or expectations enforced.
Each has pros and cons.
Program Implementation
Suggested attendees for the workshops:
Productivity is composed of practices throughout an organization. The multiple levels of the organization chart, and most if not all functional departments, can contribute.
This program, Manufacturing Productivity, is arranged to present instruction to different functions in the organization, to spread the practice of productivity widely.
Each workshop is intended for about ten attendees, chosen for their knowledge, guidance, responsibility, and strategy acumen. For a manufacturing plant, job titles could be such as Plant Manager, Director of Operations, Director of Manufacturing, Director of Materials, Director of HR, Director of Finance, Manufacturing Manager, Manager of Engineering / Maintenance, Manager of IE / Manufacturing Engineering . Process Engineering, Manager of Cost Accounting. The titles relate to a typical organization of a manufacturing plant, and the client organization or titles may be different.
The following workshop schedule is planned:
Workshop 1: Baseline assessment of the as-is situation.
The client will have received in advance a list of as-is assessment questions, and may well suggest others. The questions address a wide variety of manufacturing circumstances, because productivity is affected positively or negatively by many different factors. There are two primary objectives; one to collect information about today’s status, but also to learn what are considered to be the more important issues. Maybe even some that are not on a standard list. During the body of the workshop, the answers to the as-is assessment, and the ramifications of the answers, will be the focus of discussion, as they relate to primary management concepts within the workshops.
As the manufacturing productivity process is constructed around work measurement, the client is requested to suggest which internal department, existing or to be established, will handle work measurement.
Workshop 2: Establish or modify work measurement within the organization. A full exploration is presented, of purposes, processes, mechanisms and tools to be used in developing objective work measurement. This workshop will allow the attendees to understand work measurement and its critical place in productivity improvement; to experience some of the challenges and unique applications. It also provides the curriculum for subsequent detailed instruction of the practitioners, as they measure work, maintain accurate records, and apply results.
Workshop 3: Reduce waste, and the Pareto Principle
Reduce waste
Just what is waste? A March 2009 “Business Week” article presents this test:
Will a customer pay for this activity?
Will my service fail without this activity?
Will I go to jail if I eliminate this activity?
Answer “no” to all three, and the activity can essentially be defined as waste. Sounds good.
Pareto Principle, 20% of the elements will constitute 80% of the cost, or problems, or time. Let’s work on the most important opportunities.
Workshop 4: Productivity Constraints
Consider factors and equipment which limit client output and / or productivity. Suggest processes to identify and manage constraints. Specify frequent constraints to productivity, across the organization, and suggest improvements.
Workshop 5: Achieve outcomes, not just output.
• right product; new product development and introduction.
• in the right quantity; inventory, JIT, batch size.
• of the right quality; for the product, theory and practices through out an organization.
• at the right time in the right location; site search, plant loading, relocate, consolidate, modernize
• Appropriate metrics to evaluate manufacturing performance.
Workshop 6: Improve the workstation
Processes to improve the workplace, especially less-automated production workstations, but also the workstations in non-production groups such as materials handling, quality, maintenance.
Workshop 7: Floor reporting, scorekeeping, using production rates to set schedules.
The lead topic this session will be production department reporting currently in use; shortcomings, usefulness to management, to floor supervisors, and its timeliness. Improve the extent to which reports inform direct supervision. A second topic identifies particular work measurement data, which may be used, for accuracy and objectivity, to establish direct labor requirements current and future, such as production schedules, capacity, cycle times, effect of product mix.
Workshop 8: Changeover and interruptions to production
This workshop will focus on interruption to production, on practices and performance not only there but also within maintenance, materials management, and the quality departments. These support groups contribute to manufacturing productivity, by the ways in which they conduct their own activities. How to analyze and improve changeovers, and the processes available to assist.
Workshop 9: Product cost reduction; overhead cost reduction, profit improvement.
Remember the Pareto Principle. Institute formal Cost Reduction or Profit Improvement. Processes are available to assist, and many practical avenues are explored for cost reduction.
Workshop 10: Modern management planning and control processes, and the golden oldies.
Topics for discussion; useful modern and classic processes to optimize, the capabilities and limitations and particular areas of usefulness.
Workshop 11: Facility Planning and Plant Layout.
Arrangement of people, of materials and equipment, is at the very heart of productivity. Location and capability of operations, or Facilities Planning, sets the stage for productivity. It, and Plant Layout especially major layout are not necessary every day. But there are processes to perform major or minor projects correctly and these will be presented for the time that they are useful.
Workshop 12: Results and achievements from previous workshops. Further development of selected topics.
Summarize client action, short term and long term, and results to date. Plan the future.
Program Review
Workshop 1 initiates a major assessment of as-is activities. The first objective is to record and assess the processes which are currently in place to plan and control operations. The second is to analyze constraint activities, problems, and actual or potential interruptions to production.
For workshops 2 through 11, specific topics and processes will be presented, demonstrating facets of productivity and the manner in which they relate to each other.
The final workshop will constitute a six-hour program review session.
Workshop 2
This workshop will provide theory, technology, useful techniques, forms and practices about work measurement, so that attendees will have basis for administering it. The operating detail can later be passed on to those who will practice work measurement.
Workshops 3 through 11
Each workshop will offer one or more processes to augment productivity practices within a functional section of a manufacturing organization.
Productivity is of course of particular interest in a production section. But other functional areas can have a substantial labor element themselves, which is subject to many of the same productivity principles as a production area. Warehousing and maintenance fall in this category, perhaps quality testing, sampling, labs.
At the same time both materials planning and maintenance, by the very nature of the principles, practices and rules with which they manage their own organization, can have a direct influence on productivity in the production section itself.
The individual workshops then will be structured to address production groups, as well as indirect functions within the organization.
Results of the as-is assessment will have highlighted the unique productivity issues for the client so each process can be applied in a relevant manner.
Workshop 12
The final workshop will be dedicated to review of the activities completed and processes developed or modified during the period. Results, benefits, shortcomings, the remaining to-do list will be considered.
Industries
This service is primarily available to the following industry sectors:
Manufacturing
History
Historically, manufacturing other than by artisans began with the Industrial Revolution, and until the beginning of the Second World War was marked by only small improvements, primarily in the use of machinery to perform manual tasks. Plenty more products were manufactured thanks to such as Henry Ford and Thomas Edison, but the methods and procedures didn’t evolve quickly.
Frederick Taylor in the late 1900s was the first proponent of Scientific Management. (He knew how to use a stopwatch.) While there was some subsequent innovation, the war effort provided the incentive for major development of other sophisticated management techniques.
At that point because of the quantities of war materials needed and the sense of urgency, the US shifted into a different manufacturing gear than had been seen in history before.
The obvious factors which empowered the wartime growth were technology, equipment, number of facilities and people. Both employment and especially the number of women in the workplace grew. And of course, there was money to pay the costs. But because of the urgency of demand, management systems were developed as well, to speed output perhaps rather than to improve costs.
Now, briefly to describe manufacturing during probably it’s most turbulent 70 years in history; the period that future historians will analyze endlessly.
Following WW II, consumer demand inspired US industry to ramp up, to supply local and worldwide markets. International reconstruction spread manufacturing and introduced greater demand but also international competition. Japan in particular contributed the Toyota Production System, or Just in Time. Japan bought into statistical quality control thanks to Dr. Deming, and went from producing junk to world-class products. Meanwhile, countries with low wage rates and low environmental standards started to produce not only products in the lower price range but also some more expensive ones. Protectionism through tariffs has become common as countries attempt to protect the jobs of their citizens. Moving jobs offshore started as the first textile jobs were shifted from Britain to the US, and continues today.
In this 70-year mix has been the space age, and introduction of computerization and electronics. The rise in electronics and applications and devices has introduced myriads of new ways for consumers to spend their money.
For consumers, but also for manufacturers, evolving computers and electronics and programs have introduced the mechanisms to keep track of all the developments. A negative is that the rate of technology change that is possible is inclined to obscure the crystal ball that tells us what comes next.
Current Position
A review of the current situation in manufacturing in the United States today is different than it would have been two years ago before COVID-19.
COVID has disrupted, that is the word often used. Considering the 700,000 deaths in the US, it seems disrespectful to consider such mundane things as manufacturing problems. But with a bow of our heads, we shall.
Disrupted is a descriptive word when it comes to discussions of manufacturing issues as well. It seems particularly to apply to customer demand and supply chains. Pretty serious challenges to manufacturing, right? What comes in the front end, and who is going to buy what comes off the shipping dock?
Spatially, manufacturing is in a bit of a squeeze, because of the medical desire for social distancing. It is not so easy to spread a production line as it is to skip every other desk in an office.
International tensions currently have an effect on manufacturing as well. The supply chain is disrupted, and it is not clear just why, whether it is a result of COVID-19 or the fact that nations are squabbling or cargo ship delays. Why are there microchip shortages; is it COVID, or the shortage of rare earth elements or an under-capacity in fab shops, or international tensions? Or a portent of things to come?
Re-shoring is a consideration for companies. Bring production back home, or at least near-by. Yes, the labor price for a part may be cheaper if it comes from halfway across the world rather than the next neighborhood over, but the inventory in transit, the potential damage or obsolescence, the confidence that you have in the part being delivered on time go a long way to make up the labor cost difference. Labor is after all a relatively small part of most manufacturing costs. However, if the next-door supplier no longer has the tools, space, experience to make your part, reshoring is not so simple.
But other basic issues in manufacturing still apply just as they did before COVID-19. Some may even be amplified; for instance, there is a national interest in resigning your job and moving to a new location.
Skilled workers are tough to find, and that of course causes wage rates to rise. Supply chain disruptions will lead to unexpected changes. But these circumstances are all the more reason to adopt a consistent process of productive practices in your operations.
Future Outlook
The future for US manufacturing, even for just the next year, seems pretty fuzzy.
At best some of the effects of COVID will be reduced, and people are actually learning how to live and operate effectively even under the disruptive conditions of the last two years.
The word “agile” is bounced around a lot recently, and absolutely corporate agility is a desirable quality. Agility will be tested in near-term manufacturing because the disrupted trade situation worldwide will likely translate into more frequent schedule changes and smaller batches. Expect the supply chain to be muddled for a while yet. There may be a “new normal” in which discretionary spending patterns are modified.
And skilled labor will continue to be in short supply.
Electronics will offer more options for information and control, and that tends to be a good thing for many processes. Artificial intelligence will play a part in that change I’d guess.
More new products will likely be introduced in the future, and they may well be more technical, with more features, bells and whistles.
The Pareto Principle however will still prevail; 20% of the items will still make up 80% of whichever cost, problems, or benefits you consider.
And now we come to the major purpose of this presentation, which is to contribute to solutions of issues which are likely to occur in your short-term future. In order to make the decisions, to take the actions, which will likely be forced upon your organization by the operating constraints of 2022 and beyond, you will need information about what it is that your operation does, and in particular how long it takes to do it. Arguably the most important piece of information in management is, how long does the job take.
Work measurement is the building block by which your organization determines how long the job takes, and builds that fact into all of the processes which use time as a basic component of planning for the future, and for calculating how well you did against your expectations for output, productivity and cost.
The actual observation of the practices which occur in your manufacturing process using work measurement techniques can be as effective as the work measurement itself is. What actually happens? Is that what’s supposed to happen? Does everybody do it the same way? Is it the approved method, performed on the correct equipment, for which the rate was set in the first place?
Pharmaceuticals
History
Pharmaceutical manufacturing is a simple term, but in actual fact is composed of separate parts which are quite dissimilar. For instance, processes are very different to manufacture an injectable drug rather than a tablet or capsule. Sets and devices are assembled in a manner quite different from filling injectable solutions. Prescription formulations can be quite different from an over-the-counter remedy. Solutions compounding, or mixing, is performed in another environment completely. And any sterilization process contains a show-stopping factor. In the really old days in the United States patent medicines sold over the counter or out of the wagon; I really don’t want to know.
The major factor in pharmaceutical manufacturing in the US and much of the rest of the world is and has been the F.D.A. Obey their guidance by whatever name, period. Yes, you can write your own particular procedures, but they must ultimately meet FDA guidelines, Current Good Manufacturing Practice.
Equipment and facilities must be formally validated, tested and proven to perform as required. (When that was initially required years ago manufacturing people loved the regulation; at long last equipment was required to perform.)
Changes have been introduced all along, from materials and technology such as better filtration capability for both air and liquids, and cleanable surface finishes. More recently, labels can be read electronically. Bar codes changed the world. Change was occasionally driven by recalls, what didn’t work had to be modified.
Technology and CGMP guidelines have typically been very much in step as soon as an advanced procedure or equipment was available in the marketplace it became standard practice. You would go to the trade shows, see what’s on the market and figure out what the guidelines were likely to be next year.
Current Position
Currently, during the COVID-19 crisis, as news clips would show production of vaccine vials zipping down a line, it appears that fill and finish equipment hasn’t really changed very much recently. There may be a new variety of stainless steel and type of electronic sensor, but the equipment looks to be the same and indexing at about the same speeds. There have always been variations in filling machines; inline or circular, how many heads, solutions dropped in from overhead or pumped in. The same similarity exists in tableting equipment and processes. Electronic controls and sensors continually evolve.
A major change and complicating factor has been in the solution itself. Often solutions were prepared in the next room to filling, or upstairs. Solutions were expected to have different ingredients, complexity, viscosity, pH or toxicity but they were not as sophisticated as today’s solutions and especially vaccines.
A factor which affects pharmaceutical manufacturing has to do with batch size. Batch sizes can be limited by the clock time from mixing until filling, or by the size of the vessel in which it is compounded mixed. As a result, batch sizes may be smaller than they would otherwise be, to meet sales demands.
Substantial paperwork accompanies a particular batch change; a physical line clearance takes time, cleanups to equipment and rooms between batches tend to be quite a bit longer than in other industries.
Another differentiation that complicates pharmaceutical manufacturing is the required change in protective garments worn to maintain cleanliness. Gowning can require substantial periods of time and it’s a fact that the garments aren’t quick-change. Nor are changerooms conducive to rapid use.
Oh by the way, pharma manufacturing people are expected to meet the production schedule and the budget, pass regulatory inspections, increase capacity, perform safely and have a satisfied work force, just like their counterparts who make thumbtacks or paperclips.
Future Outlook
Future pharmaceutical manufacturing will not change dramatically if the past is any indication. Production lines may include more capable instrumentation than today as electronic technology evolves; adding a quality benefit, but regulations won’t get any easier nor requirements less stringent.
Indeed, the complexity can increase. The COVID success with an mRNA vaccine suggests the scientists will expand the practice, probably in ways not foreseen at this point. Living systems and molecular engineered products will be more complex that sugar water and saline solution.
Pharmaceutical labs develop and test through clinical trials many products which do not prove out to be successful, whether medically or commercially. This has always been a major factor in financial expectations for pharmaceutical companies. For a manufacturing plant, there is no effect from the success rate of new products. But when a clinical trial is successful and a new product is rolled out into manufacturing, there can be a startup cost and learning curve as a new process is brought in and integrated into the routine. And THERE WILL BE a sense of urgency.
The pharmaceutical industry by its very nature employs a very high degree of documentation and regulation. Not only for the research which leads to a new product, but also in the manufacturing process itself. Facilities, equipment, and methods are proposed and approved by multiple disciplines. Any change has to go through the same approval process, so there is not the same kind of ad-libbing that can occur are in other industries.
Within all this formal framework then, how does a pharmaceutical manufacturing facility improve its performance? By knowing objectively how long the job takes and improving operating performance, which is to say reducing delay, cutting the frequency of and time for changeovers, identifying the bottleneck operations or constraints and relieving them sequentially, by recognizing causes of lost line time, by addressing the unique factors such as protective clothing changing and batch changeovers.
Consumer Goods
History
The end of World War II seems to have been the starting point for the world-wide increase in consumer manufacturing. There was in the US for instance an availability of manufacturing facilities, people who were used to working in factories, a pent-up demand for consumer goods due to the war effort, and newly found technology and manufacturing strategy.
The United States manufactured for domestic consumption and for export, then as individual country conditions allowed, manufacturing was added across the world.
In many cases manufacturing was introduced into countries worldwide by multinational conglomerates; I for one was a part of that scenario. Manufacturing in these operations was typically for the local market. But over time, individual countries developed the capability to fund and operate their own manufacturing; nationalism played no little part in that decision. The next step then was for them to learn to produce so that other countries would accept their design and quality.
Europe regained both its manufacturing capabilities and its consumer demand. Asia became a major player in production, to begin with in consumer goods and then into more sophisticated products. Latin America and Africa became players in the worldwide market. Tax policy in some countries encouraged large corporations to place manufacturing in other countries.
Japan in particular contributed the Toyota Production System, or Just in Time. Japan bought into statistical quality control thanks to Dr. Deming, and went from producing junk to world-class products. Countries with low wage rates and low environmental standards started to produce not only products in the lower price range but also some more expensive ones.
Then, history repeated itself. In the early 19th century, manufacturing was transferred from one country to another. Manufacturing, largely textiles, was moved from England to be near the source of supply, cotton, in a country with a lower wage scale, America. Starting in the late 20th century, this scenario was repeated.
Technology has exploded and designers have been quick to develop new products do utilize the technology.
Current Position
Today, consumer goods manufacturing is a worldwide effort as equipment, people, and processes are available everywhere, shipping and transportation are in place, and international sales options continue to increase.
That’s the good news. The bad news is that we have been two years with COVID-19. COVID has disrupted. Considering the number of deaths, it seems disrespectful to consider manufacturing problems. But we heal, and move on.
Customer demand and supply chains are frequently described as disrupted. And that is a serious challenge. Are spending patterns of a discretionary nature also disrupted? If so and if any changes are of a permanent nature, then there can be a shift in what products are in demand.
International tensions currently have an effect on manufacturing as well. The supply chain is disrupted, whether as a result of COVID-19 or the fact that nations are squabbling or cargo ship delays, microchip shortages, the demand for rare earth elements.
For the manufacturing sector, electronics has been a major assist. Electronics are involved in measurement, sensors, controls, all elements of manufacturing design and production.
Automation continues to be possible in many manufacturing workplaces. Some, having to do with safety and workplace conditions such as welding, and painting were among the first to be automated. Whether to automate for labor cost savings is another issue entirely, particularly in low wage rate economies.
Layouts in manufacturing facilities because of COVID-19 may raise problems today. Medical advice is to socially distance, whereas productivity theory says to shorten the distance between operations.
COVID seems to have opened minds to a realization that there may be something more than just the status quo. Employees at all levels may rethink just what they are doing and why.
Manufacturing of consumer goods is well positioned across the world.
Future Outlook
The future will reward those manufacturers, I believe, who understand the processes and products within their chosen marketplace. Just exactly what are the manufacturing limitations to the company; what can they do precisely; how much does each product cost exactly; what is the output capacity; how long does it take to introduce a new product; just exactly how profitable is the company; what is the manufacturing growth plan, both short and long term?
Innovation seems to continue to produce different products on the expectation that consumers will learn to love them. Consumer manufacturing will be especially tied in with innovation, especially if products are in personal communications or internet related. An agile company can react to such factors, outside their own control but which affect their company’s success.
Technology is important to consumer manufacturing companies for two primary reasons. First, how can technology be a part of the design of the product itself? Secondly. what can technology contribute to the manufacturing process? This might be a mechanical technology that’s changed, offering new manufacturing opportunities. It might also be electronics that measure and control perhaps even artificial intelligence to understand and predict. As usual with any investment, can it be justified?
Re-shoring should be a consideration for companies. Bring production back home, or at least near-by? That will simplify the supply chain, cut transport cost ease communication and shorten cycle times. Labor is after all a relatively small part of most manufacturing costs.
Within all this uncertainty, how does a manufacturing facility improve its performance? By knowing objectively how long the job takes and improving 34operating performance, which is to say reducing delay, cutting the frequency of and time for changeovers, identifying the bottleneck operations or constraints and relieving them sequentially, by recognizing causes of lost line time.
Food and Beverage
History
Historically and traditionally, the food and beverage industry has pretty much had a local focus. Since day one, it was based on food that could be grown locally. Transportation limited the options when it came either to obtaining ingredients or to sending the finished product very far away. So, to a large extent products and marketing were both limited by how good the road was and where the river, stagecoach or camel caravan, later the railroad line, went.
In the last century however roads are better, trucks and trains run more places, amazing amounts of food products are shipped by air.
As people travel more, they often bring their dining preferences with them. Some products especially those which must be kept fresh, and those on the high end have been shipped internationally for some time.
But the vast majority of food canning plants were, and still are, located close to the raw materials which they package. The food and beverage manufacturing process has long been as extensively mechanized and automated as the state of the art allowed. Process machinery perhaps has not changed greatly in recent years, but the instrumentation and controls have become as advanced as electronic technology allows.
Regulatory bodies routinely establish standards for food and beverage preparation, and perform inspections to assure compliance. Regs specify different requirements according to the unique characteristics of the products being preserved. Recalls occur periodically, most often because the ingredients are of an organic nature, the product is not one which can be assembled out of metal or plastic components.
Travelers recognize that the favorite food from one region is not always available in another region.
Equipment and processes used to produce a beverage or can of beans or a frozen dinner or ice cream or infant formula or hot sauce or applesauce or in a bakery are completely different, often with a difference in human involvement. Containers are all shapes, made from a multitude of materials on site or far away.
Current Position
As with other industry sectors, the food and beverage industry is currently affected by COVID-19. People have been eating at home more of course, and the restaurant industry is suffering. As people eat in more, they use more purchased food products. The industry seems to have done very well in introducing new varieties of food during the pandemic. But varieties mean changeover in manufacturing, which means inefficiency. All the changeovers to produce all the categories, lo-fat, Vegan, non-GMO.
Today the food and beverage industry is not really in the spotlight as far as difficulties are concerned, nor is any particular upside anticipated. Technology is stable and proven. Tamper-evident packaging is well established, although new varieties continually appear.
Food demand is always going to be there but the specific demand by product varies. Tastes change and some products go out of style while others become popular overnight. Grocery stores don’t, can’t, stock all of the different brands and varieties that there are.
Food and beverage manufacturers still have to contend with the normal manufacturing difficulties inherent in putting ingredients into containers. There are constant time pressures due to dealing with fresh, perishable foods. Food chemistry is different and has to be controlled in a number of ways. Fortunately, technology is advancing to assist to measure and control characteristics that are unique to food preparation, as well as in the normal manufacturing process.
The supply chain is often short, local, for ingredients. But skilled labor will continue to be in short supply. Each manufacturing site will have the usual issues; employees with acceptable qualifications, job performance, the next changeover, product quality. Improvements possible include get all of the waste out, relieve bottlenecks, maintenance both preventive and breakdown, balance work loads better, set reliable output goals. Is there a promising new machine or technology or material?
Future Outlook
The future for food and beverage manufacturing seems to be cautiously optimistic.
At best some of the effects of COVID will be reduced over time, and people are actually learning how to live and operate effectively even under the disrupted conditions of the last two years.
The word-wide supply chain is in disorder we hear, but to me that should have relatively less impact in the food and beverage manufacturing sector, which traditionally have been more locally oriented.
Electronics will offer more options for information and control in the production line, and that is a good thing for many processes. Artificial intelligence may well play a part in that change.
Many new products will likely be introduced in the future if the past is any guide. (Pareto tells us however that 20% of the items will still make up 80% of whichever cost, problems, or benefits you consider.)
Batch changeover affects food and beverage manufacturing more than other industries. Substantial paperwork accompanies a particular batch change; a physical line clearance takes time, cleanups to equipment and rooms between batches takes longer than in other industries.
Another differentiation that complicates food and beverage manufacturing is the required change in protective garments worn to maintain cleanliness. This can require substantial periods of time and it’s a fact that the garments are not quick-change. Nor are changerooms conducive to rapid use.
These generalities affect food and beverage manufacturing as a whole. An individual shop floor will be concerned about more specific problems that they face today, about product flow, job performance, the next changeover, product quality.
They may be thinking also about how to do the job with less work, get all of the waste out, relieve bottlenecks, balance work loads better, set reliable output goals, make those blasted changeovers faster, assure that everyone is performing their job the same way.
Plant management will consider how to justify the new machines or technology or materials that would improve the process, find new employees with acceptable qualifications, adjust the supply chain to ensure materials supply.
Corporate manufacturing management will have its normal share of operating difficulties to contend with plus those broader issues accentuated by COVID-19 and world trade tensions. Is this the time for us to make products in house rather than buy? Do we bring part suppliers closer to home? Do we consolidate facilities? Do we need another plant, in addition to or instead of?
Fast Moving Consumer Goods
History
Historically, production of fast-moving consumer goods in many ways is not very different from the manufacture of any consumer goods. What differentiates fast moving consumer goods has more to do with marketing and technology perhaps then with manufacturing itself. And with factors as simple as the distribution of buying outlets; for instance, 7 – 11 stores bring the product closer to the homes of those who will buy and with such as Sam’s and Costco you can really stock up.
However, the mass production of fast-moving consumer goods quite commonly uses the same kind of equipment as any other canner or bottler or food manufacturer. Electronic device production for small items does not differ greatly from that of the big-ticket purchases.
The end of World War II seems to have been the starting point for the world-wide increase in consumer manufacturing of all types. In the US an availability of manufacturing facilities, of people used to working in factories corresponded to a pent-up demand for consumer goods due to the war effort, and newly found technology and manufacturing strategy. As individual country conditions allowed, manufacturing was added across the world.
The United States manufactured for domestic consumption and for export, but fresh products with a low profit margin have traditionally been packaged quite near the market where they were purchased. Fast moving consumer goods often consist of freshly grown local products, which may have a localized popularity.
Europe regained both its manufacturing capabilities and its consumer demand. Asia became a major player in production, to begin with in consumer goods and then into more sophisticated products. Latin America and Africa became players in the worldwide market. Tax policy in some countries encouraged large corporations to place manufacturing in other countries.
Current Position
Today, fast moving consumer goods manufacturing is somewhat divided into two sectors, one being the low-cost food and beverage products especially those which contain fresh or organic materials, which may still to a large extent manufactured close to the point of sale. But one sector of fast-moving consumer goods has to do with consumer electronics which as we all know are becoming less expensive. They are small and lightweight, so unit shipping charges contribute a relatively small portion of their overall price even when delivered half a world away.
Even fast-moving consumer goods are now a worldwide manufacturing effort as equipment, people, and processes are available everywhere, shipping and transportation are in place. International sales options continue to increase.
However as with all other products worldwide we are now two years into the COVID-19 pandemic. COVID has disrupted customer demand and supply chains. And that is a serious challenge to the demand for products. Are spending patterns also disrupted? Have consumer tastes shifted, will we still continue to spend as much? If so and if any changes are of a permanent nature, then there can be a shift in what products are in demand.
For the manufacturing aspect of fast-moving consumer products, there are two quite different scenarios. Electronics design and manufacture continues to evolve at a rapid pace, and that includes the small electronic items that are part of fast-moving consumer products. But traditional food and beverage manufacturing equipment is still basically pretty similar to what it has been for years now. Materials of construction continue to be improved and electronic controls and sensors are better, but otherwise there is relatively little improvement.
Future Outlook
Manufacturers who understand the processes and products within their chosen marketplace should do well in the future. Those who know their manufacturing limitations; what their capabilities are, and what each product cost is exactly; what is the output capacity; how long does it take to introduce a new product; just exactly how profitable is the company; what is the manufacturing growth plan, both short and long term?
Innovation seems to continue produce different products on the expectation that consumers will learn to love them. Fast moving consumer manufacturing will be especially tied in with innovation, for those products which are in personal communications or internet related.
Technology change is vital to this portion of fast-moving consumer goods manufacturing companies for two primary reasons. First, how technology is a part of the design of the product itself. Secondly, what can technology contribute to the manufacturing process? This might be a mechanical technology that’s changed, offering new manufacturing opportunities. It might also be electronics that measure and control perhaps even artificial intelligence to understand and predict. As usual with any investment, can it be justified?
Re-shoring should be a consideration for companies. Bring production back home, or at least near-by. That will simplify the supply chain, cut transport cost ease communication and shorten cycle times. Labor is after all a relatively small part of most manufacturing costs.
It seems that there will be uncertainty. However, a manufacturing facility can improve its performance. Know objectively how long the job takes and improve operating performance, set priorities, reduce delay, cut interruption time and frequency, identify bottleneck operations or constraints and relieve them sequentially, recognize causes of lost line time.
Locations
This service is primarily available within the following locations:
Salt Lake City
History
Salt Lake City, which is to say all of the towns between at least Ogden to the north and Provo to the South; Tooele out to the West and into Park City in the Wasatch Mountains to the east. That is modern day Greater Salt Lake City Utah.
Utah is the Beehive State, busy. From pioneer days, Utahans have utilized the fertile valleys in the mountains for agriculture, and prospered. Industry generally had to do with products which came from the farm and the tradesmen’s workshop.
The Great Salt Lake is at a very low water level, but it has never had much to do with commerce in the state. And so, it is not much of a factor historically. SLC has become the largest city in the intermountain West. The metropolitan area extends, more or less continually populated, between Ogden and Provo.
The US government has a presence at Hill Air Force Base and at the sprawling Tooele gunnery range to the West, where the latest munitions are tested.
This area has long been known for skiing in the Wasatch and for outdoor activity such as mountain biking, rock climbing, and river rafting on streams in the area. Some nice man-made lakes are nearby, with natural Alpine lakes east. An interesting point is that manufacturing which services the outdoor recreation industry has prospered in Utah.
Industry and manufacturing in the area was composed of relatively small operations with an occasional remote branch of a larger corporation headquartered elsewhere.
And then; Silicon Valley discovered Utah. In the mid 1980s Novell Incorporated, a software and services company, came to Provo. Novell was a successful company for 10 years and then was taken over by others. But the word had gotten out, in Utah you could work and then after work go skiing. Or mountain biking, rock climbing, Moab occasionally.
Current Position
Today the SLC area is known as the Silicon Slopes, so called for the startup or relocated businesses with some tie to electronics, communications, or the internet.
A multitude of relatively recent companies now operates in greater SLC, functioning in the internet services, applications, financial, telecommunications sectors. Others are biopharmaceutical or pharmaceutical, businesses.
There are other companies which specialize in outdoor activities and the equipment with which to participate. They may not manufacture here so much now, having moved manufacturing offshore.
A predominant tactic of these newcomer companies is to offer prospective employees an outstanding quality of life; the opportunity to live in Utah, which has five national parks each different geologically from the other, each spectacular. Mountains, deserts, alpine lakes are nearby SLC and accessible. The license plate says, “Greatest Snow on Earth” or “Life Elevated”. Downtown SLC is 4,226 feet above sea level, the eastern edge of the city is around 5,000 feet. Park City is 7,000.
Several remote manufacturing and warehousing facilities of nationwide manufacturers are located in Greater SLC.
In very recent years, oil-bearing shale has become a viable crude oil source. Shale deposits are being fracked some 170 miles to the east, then crude oil is trucked into Salt Lake City where petroleum refineries are in place.
Utah has recently authorized a Foreign Trade Zone to be located in the Salt Lake Valley. SLC has always served as a distribution hub for the intermountain West and this trade zone is intended to augment the distribution system infrastructure.
The state of Utah has done a good job with its Interstate system; building this year to facilitate access and extending and repairing what is in place. A new, modern terminal has just opened at SLC airport.
Future Outlook
In Salt Lake, the recovery from the COVID pandemic in the near future will be closely watched. Not so much for the local impact, but to observe how the marketplace may be changed as customer demand shifts.
Because not only manufacturers but also support businesses are located in the Salt Lake area, the comfort level of existing businesses and of potential newcomers increases with an economic recovery.
Manufacturing companies in Utah usually are not large. Except for the recent growth that created the Silicon Slopes, manufacturing companies are engaged in a wide range of different marketplaces This diversity is good in that the success of manufacturers depends on different segments of the economy.
Local governments express they are interested in building the industrial and technology technological bases and results support their claims.
Many states, officially or not, encourage companies in California to relocate to their states. (In October 2021 Tesla announced its intention to move to Texas.) Utah seems to engage in this practice as well, as evidenced by the number of newcomers into the Silicon Slopes.
Utah’s history as a center of business in the Mountain West has led to the development of such infrastructure as interstates and recently the foreign trade zone in Salt Lake City. This is likely to continue in my opinion.
The natural draw of Utah is its outdoor lifestyle, and that is certainly impressive. People who choose to place quality of life high on priorities will frequently find their way to Utah.
The unemployment rate in Utah traditionally is quite low so the demand for skilled labor, and rising labor costs will be facts of life for manufacturing.
People continue to move to the area as is evidenced by the recent boom in housing construction.
San Diego
History
San Diego first came to the attention of the world during the early days of World War II. A large part of the wartime aviation industry was located in Southern California, of which San Diego County had its share. A deep-water U.S. Navy base was and is located in San Diego. A Marine base, Camp Pendleton, is the last word in modern amphibious warfare.
The industrial base was strengthened by companies established to feed component parts to the aviation assembly operations. But, mid century, we mostly heard from San Diego concerning the beaches and the surf. The fact that there was industry in San Diego seemed to slip our notice. The movie “Top Gun” brought attention back to San Diego but not for industrial reasons.
Meantime, newcomers were constantly drawn by the living ambiance of San Diego, the temperatures, and the beach. The Gaslamp Quarter, Little Italy, Balboa Park. La Jolla. Torrey Pines. Tourists came, then returned to live. Among newcomers were entrepreneurs, who wanted to take part as well, to start their own business and corporations.
The manufacturers who were here all along expanded and their presence attracted vendors and support functions. The electronic industry came to serve aviation, and the U. S. Navy made San Diego it’s base for Pacific operations. Maritime related industries came to San Diego because of the Navy presence and because of rising interest in private boating including large offshore yachts.
Pharmaceutical manufacturers started to come to San Diego. Since companies with similar technology will congregate over time, San Diego industrial size and capability has continued to increase.
Current Position
San Diego today can be described as a a) Navy, b) international, c) Southern California, d) beach, e) Silicon Valley, f) tourist, g) historic, h) university, town; correct on all counts. But it is also a major manufacturing center.
The City of San Diego fills us in: 14 advanced industries produce $42.1 billion and pay $116,600 / year on average; 1,200-plus Sports and Active Lifestyle companies operate in the region.
The city lists International Trade, Manufacturing, Military, and Tourism as primarily responsible for economic impact. A primary part of international trade is the Port of San Diego, the only deep-water port on the west coast. That proximity to an ocean port will be a major benefit to some companies.
Another source rated San Diego as the fourth largest US city for pharmaceutical manufacturing.
San Diego has been successful, and should continue to be successful, not just because of one particular company or public institution but because of the cooperation and interaction between different public and private entities.
San Diego is the home to a large base of wireless cellular technology companies. The state of California years ago promoted collaboration between the wireless industry and life sciences because significant electronic technology, and pharmaceutical research, businesses were located here. A combination of public and private educational and international research institutions in the area have cooperated over the years particularly in biopharmaceutical and medical device research. As a result, life sciences industries employ perhaps 50,000 people.
The county is named San Diego as well, it is on the Pacific Ocean, against to Mexican border to the south.
At 1.37 million people plus, San Diego is the eighth-largest city in the United States and the second largest in California.
Future Outlook
San Diego should continue to thrive. It does many things well. It let the football Chargers get away, but most everything else has succeeded.
As electronics technology continues to evolve, and as the biopharmaceutical industry grows from its early stages, San Diego will be in the forefront of research and innovation and cooperation in these categories.
The list of manufacturing companies represented in San Diego is quite impressive. There are big names in pharmaceuticals, electronics, biopharmaceuticals. There is, in addition, the broad base of companies going back to the WW II days. Industry prefers to move to a location where there is a concentration of business already, because there will be the infrastructure of suppliers, vendors, repair shops that will help the newcomer in its operations. The existing industrial base could well attract other potential players into the mix.
The list of public and private research entities is also impressive and has produced results by its actions and cooperation with industry already.
Add to this the factors which brought people to San Diego in the first place, the climate, the beach. The future for San Diego should be full of opportunity.
The beachfront is already spoken for, and the city itself is limited geographically. The downtown is relatively small and squeezed between Balboa Park, freeways, and San Diego Bay.
There are delightful neighborhoods in the city, and towns around. And traffic is fierce on the freeways, but surface streets are good; housing prices are a bit steep, otherwise costs are not too bad.
Dallas, Texas
History
Dallas, founded in 1839, and Fort Worth ten years later, were initially separate and distinct towns, and still are technically. There is plenty of civic pride remaining. And long ago, Fort Worth was a cowtown, while Dallas was more industrialized. Railroads were at the center of the early prosperity for both. But with Arlington situated between them, the area has become number four in population in US metropolitan areas.
Dallas / Fort Worth is in a relatively flat part of Texas. By the map it occupies an area some 60 miles east to west and 40 miles or so north to South. Of course, that area is not completely filled. Even if your short-term destination is in the area, you may still have quite a drive to get there.
Dallas / Fort Worth is east of the major oil field activity in Texas, so there is not extensive oil-patch related business here. The financial sector is however quite connected to oil.
World War Two brought major manufacturing to Dallas / Fort Worth, primarily to build military aircraft as well as military wheeled vehicles. Semiconductors were manufactured quite early in the area as well.
Constant change has been visible, in the skyline, in the streets and endless expressways, and in manufacturing. This has always been “Big D.”
Dallas / Fort Worth is fairly centrally located in the United States so some companies will have come here in order to produce, then ship to Western markets. It is of course a good-size market in its own right, with some 8 million people. As Dallas has grown, additional resources in services and vendor have continually evolved to serve the expanding market.
There is not a substantial military presence.
Current Position
Today, reviews of the Dallas manufacturing situation included
“Indicative of solid output growth”
“Perceptions of broader business conditions were mixed”
“Faster employment growth, longer workweeks.”
“Thirty-six percent of firms noted net hiring, while 9 percent noted net layoffs.”
“Prices and wages continued to increase strongly.”
COVID has had an effect on Texas as you may have read. But while businesses may have been closed or underutilized, the operations are ready to resume business as usual.
Most if not all industry sectors have operations in Dallas / Fort Worth; covering everything from farm and ranch equipment (this Is still the West you know) to the most modern biopharmaceutical and electronic elements and aerospace; defense manufacturers. Major US firms and international corporations have facilities in Dallas / Fort Worth. They represent leading state of the art technologies, for both traditional and modern manufacturing. Some 286 thousand people are employed in Dallas in the manufacturing sector.
The area has the third-largest concentration of corporate headquarters in the United States and is the headquarters of three of the top-ten largest Fortune 500 companies by revenue.
Interstate highways lead away; down I-35 is Laredo and the Mexican border, and the Dallas connections with Mexico are deep indeed. I-45 leads to Houston and the open sea. I 20 goes east and west. DFW airport has flights domestically and internationally. And Love Field still thrives.
Industries are most comfortable in an area with other manufacturing operations. There will be services, sources, vendors and contacts available in the area because of all the other industrial residents. As Dallas grows, there will be additional resources from which to draw.
Future Outlook
COVID-19 has affected the area and Texas, but it is cautiously believed that threat will diminish. As with most other metropolitan areas the crystal ball indicates that customer demand will increase for products across the board, which will translate into a resumption of normal business activity. For Dallas / Fort Worth that will mean a vibrant economy and significant activity in the manufacturing sector.
Dallas / Fort Worth has been connected with cutting edge companies in aviation, computer chips, and biopharmaceutical manufacturing as those fledgling industries grew, and they now have become mainstays of the economy. because these companies are here, they will continue to attract allied support organizations.
Dallas / Fort Worth has an impressive amount of infrastructure in place to support existing manufacturing and attract newcomer companies. But the area can also reasonably expect the same issues in their future manufacturing operations as other locations; namely skilled labor will be in short supply and labor rates will tend to rise.
The existing base of industry in Dallas in itself indicates that the local manufacturing economy will be successful in the future. The invested base of assets is a significant value to the company that has it in place already.
The physical location of Dallas is a distinct asset as well. There are traditional, close ties to Mexico and the border is not far away, Dallas is not a seaport but just down the highway is Houston. The central U S location tends to reduce distribution coast. DFW airport connects internationally as well as being a hub for flights in the US.
Los Angeles
History
What can you say about Los Angeles that hasn’t already been said? This is LaLa-land, Hollywood movie studios. major big time tourist attraction. But it is also an industrial complex, in all senses of the word.
Perhaps it is best to start with the location of Los Angeles. On the Pacific, it always has been a very busy port city, a gateway to the Orient as they say. Actually, two ports, Los Angeles and Long Beach. With the growth of Asia as a trading partner over the last several years, the port has become more significant than ever and as we speak is backed up with cargo ships waiting to be unloaded.
LA is also only 130 miles or so from Mexico and as a result has long standing industrial ties to that country. Newcomers to the US provide links to their home countries around the world.
During the Second World War, military aircraft production started in Southern California, partly because of the number of allied manufacturing plants, vendors, located there and also partly because of the warm weather that made it practical to train pilots. As a result, airports proliferated as well, leading to LA’s position in transportation.
Aerospace is still a leading industry, and biotechnical companies abound as well as more traditional pharmaceutical companies. All in all, this manufacturing contributes to Los Angeles County’s primary spot in US manufacturing jobs.
Third party manufacturing plants became quite popular in the Los Angeles area during the latter half of the 20th century. And of course industry acts to attract other industry; if there are vendor plants located nearby, or service
Current Position
The geography that accelerated the growth of Los Angeles industry and manufacturing in the past has not changed. The sun still shines, the beach is nearby, the temperature is warm. (usually). Yes, the ground still moves occasionally, and it is dry here like the rest of the West, but traditionally it has been relatively easy to attract people to live and work in this part of the world.
The geographic center of course is Los Angeles County, but San Bernadino and Riverside counties to the east, Orange County to the South, and Ventura to the north each provide large and vibrant manufacturing entities which facilitate doing business in the area, and residential communities from which to staff industry. Even the City of Industry, no less.
The two major ports are busy today, perhaps busier than ever before. There is in place a trained, experienced, multicultural workforce to operate the businesses which have proved successful both domestically and internationally in the past.
The size and diversity of manufacturing in Los Angeles continues to facilitate the ability to manufacture in the area. There will be resident ventures in the area which provide the goods and services needed on an everyday basis to operate, there have always been a number of third-party manufacturers, and other companies might be vendors or third-party manufacturers. Available transportation can move product anywhere, in or out.
Manufacturing in Los Angeles continues to consist of companies with basic processes. But technology is well advanced here as well, with cutting-edge, state-of-the-art manufacturing businesses in the biotechnical, aerospace, and pharmaceutical categories. Film-making studios receive plenty of attention, but surrounding and supporting the major players, a multitude of specialized entities operate successfully within their own product niche.
Future Outlook
Los Angeles in the future should have a secure economy, if history is any guideline.
As Los Angeles and the rest of the world recover from the negative effects of the COVID19 era, as more businesses reopen their doors, as people feel freer to move about, and most significantly as national and worldwide demand for products increases, we will have a better view of the future.
Los Angeles has a wide, diversified range of industries in place already.
The seaport and the volume that it handles may be an early harbinger of how the COVID rebound will proceed. Nationwide, seaports are crowded but it remains to be seen just how international trade will be realigned in the near future, if at all. But definitely the infrastructure of the port itself is a distinct asset to Los Angeles and the surrounding area.
Manufacturers in the area will face similar operational issues in the future to other locations; rising labor rates and skilled labor shortage. The problems may be simpler than other locations, as Los Angeles’s metropolitan population is very large, to ease manufacturing constraints of labor availability.
It is possible of course that the present difficulties with the length and complexity of supply lines for manufacturing will have an effect on the economy of Los Angeles. But the manufacturing economy today Is large and diverse. Substantial components that make so much difference today, namely biotech and aerospace and pharmaceutical company, are established.
Los Angeles is still the home of many people with ties to countries around the world. If there is a major shift in the supply chain, leading to reshoring of products, Los Angeles is in an excellent geographical position to take advantage of such a trend.
Irvine
History
Irvine California, in Orange County. An integral part of SoCal, close to the beach, warm and sunny, traditionally a destination as you Go West.
Los Angeles is to the north, then Anaheim and Santa Ana which are also in Orange County. Dozens of corporations are headquartered in Irvine. It is likely that the quality of life has played a major part in their decisions. After all, one of the tenets of facility relocation, and facilities certainly include headquarters, is “where does the boss want to go?”
Irvine recognized as early as the1960’s that rapid growth was likely to occur, so they planned this city in order to mitigate some of the growth pains. Irvine was largely ranchland and agricultural before SoCal started on to its popularity and subsequent growth phase.
Manufacturing is distributed through Orange County, but the primary economic driver in Anaheim is Disneyland and other Walt Disney related activities. Industry is composed of several different segments, ranging from basic industry to quite modern technology. The area is crisscrossed with highways, contains John Wayne airport, and is just south of the expansive Los Angeles and Long Beach seaport facilities. The population contains a sizable Asian component, as would be expected from a major West Coast city.
The proximity of Anaheim and Orange County to greater Los Angeles and to San Diego to the South (on the other side of the huge U. S. Marine base), has played a very favorable role in economic development. Industry and manufacturing prefer to be situated in an area where there are potential vendors and service providers.
Current Position
The city of Irvine at present has been chosen as a headquarters for dozens of corporations in a varied mixture of business categories. Manufacturing employs about 13% of the labor force, distributed among both large and smaller manufacturing plants. Local ownership controls many of the facilities, but others are part of US nationwide, and international, organizations.
Orange County is home to Disneyland, and tourism and entertainment are primary parts of the economic picture.
COVID has had an impact in So Cal, as everywhere. And the area has experienced ups and during the pandemic, as everywhere. But traffic in Southern California indicates things are back to normal. If all of those drivers applied for the open jobs here, we’d solve two problems at once.
Technology plays a distinctly favorable role in the economy of the area. Bio-tech manufacturing has built on the long-standing pharmaceutical presence, Telecom and internet related manufacturers are present. Vendors to these sectors have set up nearby. Well qualified employees work daily operating the technology involved in the manufacturing processes.
Irvine made at least one list of the Best Cities to Live in America in 2021.
The economy definitely is bolstered by the West Coast location, and by the seaports in Long Beach and Los Angeles which handle some 35% of world traffic.
The 2021 backup at these ports, as container ships wait offshore to unload, is well known. The reasons seem to involve pent-up US demand, perhaps a shortage of resources due to COVID factors, a possible re-positioning of supply chains, international tensions.
The overall make-up of Southern California business is not currently affected by the port situation. But the import path of goods from Asia lies through So Cal to a large degree.
Future Outlook
Irvine and Orange County’s economy in the future will be aided by the wide a wide range of diversified industries in place already.
The view of the future will improve as the world recovers from the negative effects of the COVID 19 era, and businesses reopen their doors and as national and worldwide demand for products increases.
Southern California and its Asia-oriented international trade, and the seaports may be an early harbinger of how the COVID rebound will proceed. Nationwide, seaports are crowded but it remains to be seen just how international trade will be realigned in the near future, if at all. But definitely the infrastructure of the port itself is a distinct asset to Irvine and the surrounding area.
If there is a major shift in the supply chain, leading US companies to re-shore products, Irvine is in an excellent geographical position to take advantage of such a trend.
Manufacturers in the area will face similar operational issues in the future to other locations; rising labor rates and skilled labor shortage. The problems may be more manageable than in other locations, as the So Cal population is very large, to ease manufacturing constraints of labor availability.
Perhaps future difficulties with the length and complexity of supply lines for manufacturing will have a negative effect on the economy of Irvine. But the manufacturing economy today Is large and diverse. Substantial trade components that make so much difference today, namely biotech and aerospace and pharmaceutical company, are established. SoCal seems well equipped to manage the possible shifts of the future.
Program Benefits
Production
- Work measurement
- Labor efficiency
- Constraints management
- Workload balance
- Methods standardization
- Manufacturing reporting
- Changeover completion
- Personnel assignment
- Cost reduction
- Capacity utilization
Management
- Production forecasting
- Reduced cost
- Schedule attainment
- Problem prioritization
- Processes control
- Outcome analysis
- Plant loading
- Indirect labor
- Cycle time
- Facility planning
Finance
- Standard costs
- Variance analysis
- Labor requirements
- Metrics reliability
- Production reporting
- Equipment justification
- Overhead allocation
- Labor costing
- Improvement evaluation
- Profit improvement
Achievements
Sylvania Electric, now part of Osram Sylvania Inc.
This plant, one of several satellite manufacturing facilities, produced light bulbs of different types during the period for which I was the manager of industrial engineering. The facility was well managed, stable, a desirable place to be employed, and profitable.
A successful cost reduction / profit improvement program was in effect for management, and an employee suggestion program for hourly. Direct employees were covered by a labor incentive system. Products were often relocated from one facility to another with the resulting need for layout revisions and new sets of documentation and rates. During the period, three different union representation elections were held for which all of the programs mentioned were subjects. None of the elections was successful.
ITT Latin America
ITT Latin America consisted of large manufacturing facilities in five countries. This was during the time that Harold Geneen led ITT, and turned in many successive years of sales and profit growth.
In this conglomerate, a central control structure was based in New York, but geographic areas had a formal structure as well, to administer standardized control programs in manufacturing, finance and quality.
Each of the five companies operated its own industrial engineering group which administered work measurement programs within manufacturing. During this time ITT LA introduced work measurement, planning and reporting into the half of the workforce which installed the electro-mechanical telephone equipment produced in the plants. Operations staff routinely visited both manufacturing and installation facilities to assist with problem areas and advise on productivity concerns, from our base in Buenos Aires, Argentina. My responsibility on LA Operations staff was for industrial engineering.
Abbott Labs, Pharmaceutical Division
Pharmaceutical manufacturing by its very nature is well defined and processes are closely controlled. The Abbott satellite plant in North Carolina was no exception; I was IE manager for two years and operations manager for small volume parenteral injectables for two years, having the opportunity to put productivity improvement into practice firsthand.
During the time, the FDA was rigidly enforcing Current Good Manufacturing Practices. The FDA in their inspections were actively trying to upgrade the state of CGMP in the pharmaceutical industry and they were successful.
One challenge to manufacturing was that occasionally product demand would jump because a competitor was shut down by the FDA. Our plant was not shut down despite rigorous inspections, back-to-back. The facility was productive, profitable, and a reliable supplier. The plaque on the wall of all the manager offices said “Results Count”.
Ray-Ban, when they were still a division of Bausch & Lomb
Ray-Ban, During the years that I was there, was a great place to practice the techniques of productivity. Sunglass business was growing at around 20% a year for four years. State-of-the-art R&D technology led to new products, an acquisition contributed, additional and more modern equipment at two manufacturing plants was installed, two more facilities were added including a maquiladora plant. As director of industrial engineering, I had several assignments but the main one was “don’t let us run out of capacity”.
Employees understood the products of the company and their reputation in the marketplace for style and quality, which definitely contributed to motivation.
Granted, sales got a big boost from movies such as Risky Business and Top Gun. But division wide productivity enabled the output to meet the sales. The plaque on the office wall of executives said The Best of the Best.
Alpharma Inc.
Alpharma Inc. is part of a generic pharmaceutical company, and occupied U. S. headquarters in Baltimore at the time, and manufacturing facilities there and in three remote facilities. They retained me as a consultant because of their objective to relocate and upgrade two remote facilities into the third. Alpharma management, with experience in manufacturing of injectable pharmaceutical products, was well versed in the benefits of productivity, and incorporated it into all of their relocation and upgrade activity. Alpharma subsequently instituted productivity improvements in manufacturing in day-to-day fill and package, manning, equipment selection, scheduling, layout, and testing labs. During the time, a primary distribution center was equipped with modern electronic communications and order processing equipment.
More detailed achievements, references and testimonials are confidentially available to clients upon request.
Client Telephone Conference (CTC)
If you have any questions or if you would like to arrange a Client Telephone Conference (CTC) to discuss this particular Unique Consulting Service Proposition (UCSP) in more detail, please CLICK HERE.